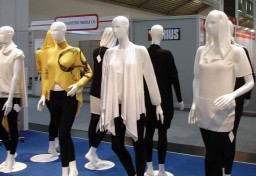
Conventional sweaters can be produced by sewing together the various parts, knitted separately, such as the front body, back body and sleeves. A new method of knitting is made possible by using the state-of-the-art computerised flat knitting machines, where an entire garment can be created in one piece, straight off the machine, without the need for linking or sewing. Such type of knitwear are generally referred to as ‘complete garments’ or ‘seamless knitwear’.
With the technology of ‘Seamless’ Knitwear machines becoming ever more sophisticated and versatile in product designs, Niki Tait takes a look at some of the innovations in the market.
Niki Tait, C.Text FTI, FCFI heads Apparel Solutions, (www.apparelsolutions.co.uk) which provides independent assistance to the Apparel Industry in the areas of manufacturing methods, industrial engineering, information technology, quick response, etc. Tel/Fax +44 (0) 1237 423163 E-mail: nikitait@ apparelsolutions.co.uk
By producing an entire garment in one complete piece, there is much potential in time and cost savings, under this production technique. There are no labour-intensive cutting, sewing or linking processes.
Besides, there is no material waste as the scrap material that is thrown away after cutting out each pattern in conventional production is eliminated.
Being computerised, the technology can be applied to a small-lot production, with greater variety, or even single item production for creating one-off made-to-measure knitwear.
Many experts in the knitting industry agree that complete garment knitting will become the mainstream method of knitting during the 21st Century.
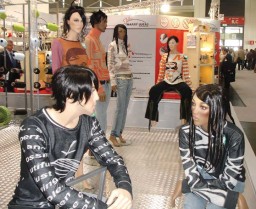
Since each garment is produced in its entirety based on digitally programmed data, item-to-item and batch-to-batch quality, even for repeat orders, it would remain consistently high throughout. Other benefits include improved stretch and mobility with the elimination of bulky, uncomfortable and unsightly seams. Drape is enhanced, as there are not many seams to alter the flow. The seams even cannot be broken down. Hence the quality is improved. Seamless one-piece construction also means that the entire garment has the structural integrity of a single piece of fabric allowing stress to be distributed evenly.
In essence, complete products are knitted in tubular form – one wide tube for the body and two narrower tubes for the sleeves. These tubes then need to be automatically connected together at the neck, shoulders and under the arms, by the knitting machine. This results in a commercially viable sweater equalling or even surpassing conventional knitwears, especially in terms of product variety, quality and fashion potential.
Shima Seiki, considered the ‘Pioneer’ of this technology, was the first to launch its patented WHOLEGARMENT technology in 1995. This technology enables three-dimensional shaping of garments, which conform better to the body shape
Shima Seiki, the pioneer of this technology, has spent over twenty years researching and developing this machinery and expertise, trade marking its system WHOLEGARMENT, which it first launched to the industry at ITMA 1995. WHOLEGARMENT has resulted in the application and ownership of approximately 150 patents worldwide.
The company claims that these patents and the mechatronics technology, besides the computer programming know-how and knitting techniques which they embody, distinguish WHOLEGARMENT from other forms of complete garment knitting industries. Shima Seiki’s dedicated technologies include the four-needle bed configuration, twin-needle arrangement, slide needle, contra sinker, transfer jack, loop presser, stitch presser, pull down device and digital stitch control.
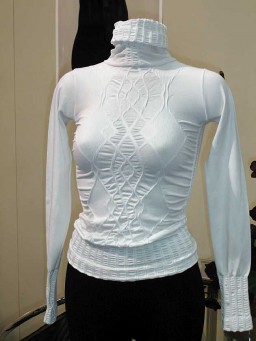
With the pull down device, for example, a computer-controlled takedown system pulls the fabric down while knitting, with precise control over incremental tension across the entire garment, on both the front and back. This permits three-dimensional shaping of WHOLEGARMENT items by allowing, for example, shoulder lines for set-in sleeves to be positioned over the shoulder towards the back, resulting in a more dimensionally accurate garment which conforms better to body shape.
The SlideNeedle is an entirely new needle design. It aims to replace the 150-year-old design of the traditional latch needle enabling unprecedented stitch designs. A flexible two-piece slider mechanism splits and extends beyond the needle hook for increased potential, especially in complex transfers. Using the slider mechanism for transfer effectively eliminates the transfer clip, allowing the needle to be mounted in the centre of the needle groove thereby achieving a perfectly symmetrical loop formation for knitting the highest possible quality fabrics.
The new Contra Sinker actively offsets, and consequently reduces, the total amount of movement of the SlideNeedle with a counter-movement. The shallower angle of approach distributes yarn tension more evenly, reducing scuffing and thereby preventing yarn breaks. Thus, together, the SlideNeedle and Contra Sinker are said to achieve better quality whilst using a wider variety of yarns, as well as significant improvements in productivity.
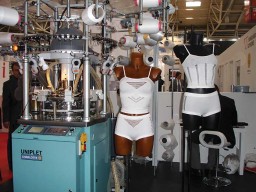
The SlideNeedle is capable of a 12-way technique, which effectively doubles the number of knitting techniques over the traditional six techniques of knit, tuck, miss, transfer, receive and racking. The six new techniques enabled by the SlideNeedle are lateral transfer, split stitch lateral transfer, split stitch front and back, second stitch, inlay and holding which enable more flexibility for knitted-in pockets, collars, buttonholes and other trimmings than ever before. Details such as darts and pleats can also be knitted in, as Shima Seiki claims, WHOLEGARMENT is the only method which allows a complete, three-dimensionally shaped and fitted garment to be worn straight off the machine.
Practical results from the new SlideNeedle design are increased stitch variation, a wider range of possible gauges and ‘gaugeless’ knitting, whereby a variety of gauges can be knit on a single machine into a single garment. This opens up further possibilities for a wider range of knitwear including cooler, more lightweight items helping to shed seasonal perceptions toward the traditional knitwear period, and enabling knitwear to be worn throughout the year.
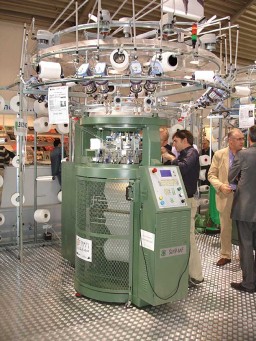
Patterning techniques such as Milano rib, inlay, and pleated, flared skirts expand knitwear’s capability to encroach on the area of woven fabrics. Shima Seiki speculates that so far it has only touched upon less than 1% of the SlideNeedle’s full potential, there being many unexplored possibilities. It further explains, with the conventional needle using every combination of the six-way technique, there are 6 x 6 or 36 different possibilities. The twelve-way technique, made available by the slide needle, allows 12 x 12 or 144 different possibilities enabling new stitch types, new patterns, new effects.
Unlike the conventionally knitted sweaters, the seamless process allows patterns and designs to remain uninterrupted across the entire garment – from front to back, over the shoulder and down the sleeves. Everything from hats, scarves, shoulder warmers, cardigans, vests, jackets, coats, jumpsuits, dresses, skirts, leg warmers, tights and socks can be knitted in their entirety. Current trends for fashion wear are for increasingly finer gauges, thus narrowing the traditional divide between fully-fashioned and circular knitwear.
Wholegarment technology is also expanding into the automotive and aeronautic industries, particularly in terms of seamless seat covers, and into the medical industry where elastomeric yarns can be used, enabling shaped support garments to be produced. Shima Seiki offers six different models of WHOLEGARMENT knitting machines.
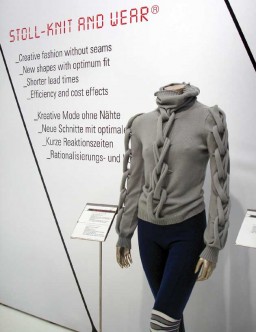
The closest competitor to Shima Seiki WHOLEGARMENT knitting is Stoll Knit and Wear. Launched in 1997, the company also feels that the potential of its ‘knit and wear’ technology is just being guessed at! There is a complete change in mindset from just considering traditional but seam-free products to utilising the machines’ full potential. Stoll puts its main strength to its flexibility in using different types of yarns, of varied thickness, its ability to knit different parts of the garment at different lengths, with different number of rows of knitting, besides its design software. There is a database of many different designs and styles on the internet, which customers can download and adapt to their own needs. Stoll offers five different knit and wear machines.
M1 Plus® software from Stoll is a material planning and control solution, which offers functions such as knit and loop simulation to allow the user to check for potential problems ahead of time. Using “M1 Plus®”, one can make the front, back and sleeves together in one piece of garment. It also offers pattern making, grading and marker making for flat knit fabric. The M1 Plus® highlights simplified pattern design with Design Mode for easy drawing, new and enhanced drawing functions. Only one drawing layer simplifies the editing, especially for Fully Fashion individual knitting-technique. The software further defines color arrangements for knitting sequences manually and easy pattern data management and maintenance. It interfaces with Eneas Design Software Shaper.
Santoni has become the market leader in seamless knitwear production, reducing traditional production costs by up to 40%
What circular knitwear specialist Santoni calls ‘seamless technology’ does not exactly mean 100% seamless as it does with flat knitting technology, however it does reduce the need for up to 90% of seams, claim the company. Developed from technology used to make socks, by producing a tube of the appropriate diameter circular-knitting machines eliminate the need to produce and then sew together pieces of cloth, thus making the side certainly seam obsolete.
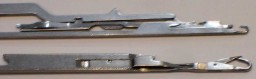
From 1999, Santoni began focusing solely on seamless machine production. It developed machines which offered more flexibility in designing patterns, producing three dimensional products, single and double jersey, levering a true mosaic knitting process, besides producing true fish net sport and fashion garments in single jersey, with zero waste. As a result Santoni has become the market leader in circular seamless knitwear production. This technology can directly produce nearly finished products, and reduce traditional production costs up to 40%. Claimed benefits include a better, comfortable and wider range of various body sizes apparels at an affordable cost.
The performance features that are linked to the combination of fibres include smooth, streamlined and sleek engineered zones of support, compression, ventilation, or shaping; ability to transition from one yarn type to another without seaming; design flexibility, styling comfort and durability with attractive appearance. In terms of production, circular seamless knitwear has also claimed to reduce labour costs, requiring fewer machines and a smaller work space, lower energy costs, reduction in yarn and fabric use per garment.
Mainly used till now in the sportswear, swimwear, underwear and medical fields, Santoni’s research has shown that seamless apparel construction can focus on supporting muscles and areas where they need it the most. An engineered fit, micro massaging features, and performance innovation, result with a blending of various technical fibres and yarns. Underwear produced on seamless machines blends comfort, fit and versatility. According to Santoni, ‘These yield high performance, seam-free, easy care, silky smooth garments that feel similar to one’s second skin and are designed to be worn under today’s fluid, lightweight apparel’. Studies have shown that once a consumer has purchased and worn a seamless garment, there is a high rate of his purchasing it again.
Santoni offers nine different single jersey machines and two double jersey models. Although the trend has been for finer and finer gauges, its latest offerings are designed to compete with the flat bed knitting industry, which enables to offer seamless fine gauge fashion jumpers, knitted up to three times quicker than the fully fashioned machines can produce.
Merz Maschinenfabrik GmbH is a company, 60% of which is owned by large diameter circular machine company Mayer & Cie, which has been manufacturing circular knitting machines to produce medical stockings. Four years ago it developed this expertise to produce a body size seamless machine, the MBS Merz Body Single, which was presented for the first time at the ITMA 2003, which works using a mono-magnetic needle selection system. The latest version, the new MBS 11, is an eight feed single jersey circular knitting machine, which is available in diameters ranging from 13 to 17 inches and in gauges from 16 to 32G.
Each feed has nine yarn fingers, four of which are with float position. With three-way technique the machine is suitable for the seamless production of underwear, swimwear, sports fashion, medical compression garments, etc. whilst the particular needle construction is designed for working with both special synthetic and cotton yarns. Besides plain garments it is possible to knit plated patterns, crocket look, and micromesh and support structures.
The integrated transfer appliance allows the knitting of double and elastic welts. Machines can be equipped with the hosiery method of pneumatic garment ejection, or electronic takedown of garment panels.
Charlotte is an eight feed single-cylinder seamless body wear circular knitting machine designed by the Uniplet Group, a Monarch company, for the production of underwear, swimwear, sportswear, outwear and medical wear with possibility of single or double transferred welt and separation of each single garment. Depending on yarn types, the structure of the knitted fabric and the diameter of cylinder, maximum-running speeds of between 85 to 140 RPM of the needle cylinder can be achieved. It has a gauge cylinder of 24E to 28E, cylinder diameter of 12 to 20 inches, a yarn finger count of 56 made up of eight feeds with seven fingers each and individual mono-magnetic needle-by-needle selection with three-way technique in all eight feeds or four-way technique in four feeds.
Plain knits, all kind of tuck, float, terry, miss-knit, cut-out patterns, logo motive and its combination can be produced with the possibility of knit-in or lay-in bare or covered elastomerics. The machine can knit yarns from 17/1 dtex to 200/1 dtex. The Uniplet Group is a Czech company, which was established, in 1949 producing sock and ladies hosiery machines. The Charlotte was launched in 2007. According to Uniplet, its key features are its ease of use, its simple and stable needle selection and the simplicity of its electronic controls.