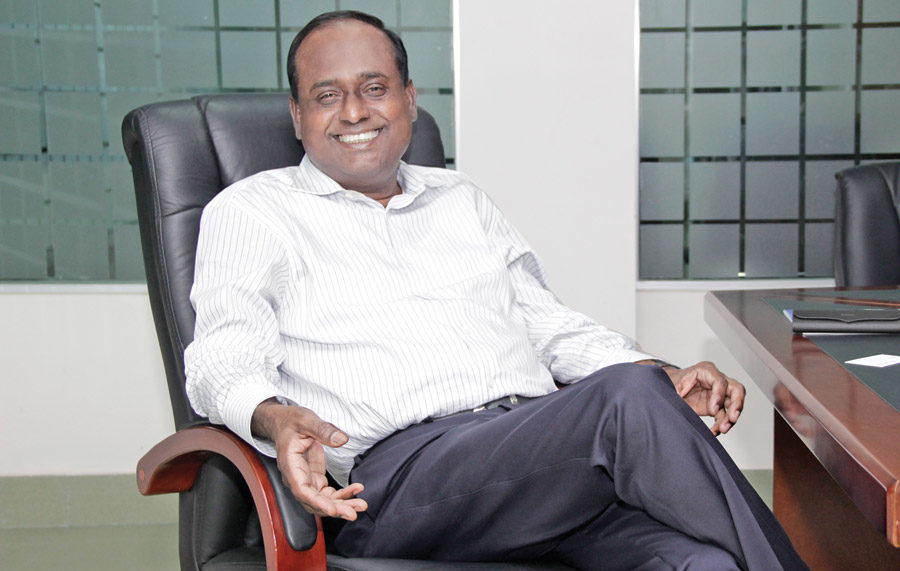
News on new factories in apparel manufacturing does not attract much attention from the industry because of its already burgeoning nature. However, when a company establishes a shirting fabric manufacturing plant, the industry celebrates because every new non-denim woven fabric manufacturing plant brings Bangladesh one step closer to becoming self-reliant in woven fabric. Contributing to the effort, Silver Line Group has set up its state-of-the-art shirting fabric unit in 2013, which can produce 36 million metres of fabric annually at full capacity. “Bangladesh has set up enough capabilities for knit fabric manufacturing and processing, and even for denim fabrics to a certain extent but we are still dependent on China and India for woven non-denim fabrics. My aim was to not just manufacture fabrics but to do the same in a setup similar to the infrastructure of the mills in these countries,” states M.A.H Salim, Managing Director, Silver Line Group, sharing his vision with Apparel Online.
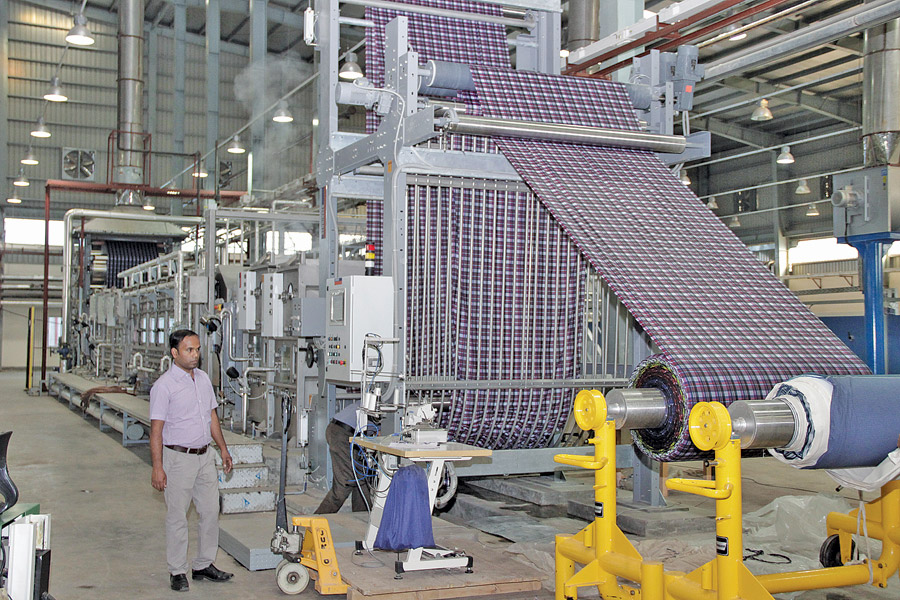
Set up in 2003 as a spinning unit, Silver Line Group established Silver Composite Textile Mills in an area of 70 acres with 129 looms and capacities for yarn & fabric dyeing, warping, singeing, desizing, bleaching, mercerisation, printing, sanforising and micro-sanding. Plans are there to have a total of 225 looms, but the same will be done in phases based on the demand. Presently specializing in yarn dyed fabrics, the company has plans for replicating the same in solid and printed fabrics. Silver Line has already started catering to Indian, Japanese, Russian and European buyers sourcing from Bangladesh.
The real achievement lies in establishing a fabric unit with significant capacity in a time when every textile company has put expansion plans on hold because of the non-availability of new gas connections. “We are still not getting gas and our facilities are running on electricity. But we will have to look for an alternate source of energy such as solar energy because we don’t know till when the gas problem will be solved,” shares Salim. However, the company already has interventions in place for minimizing its energy consumption. It has Toyota JAT810 air jet looms, equipped with a new weft insertion system, which enables 20% reduction in air consumption compared to the previous models.
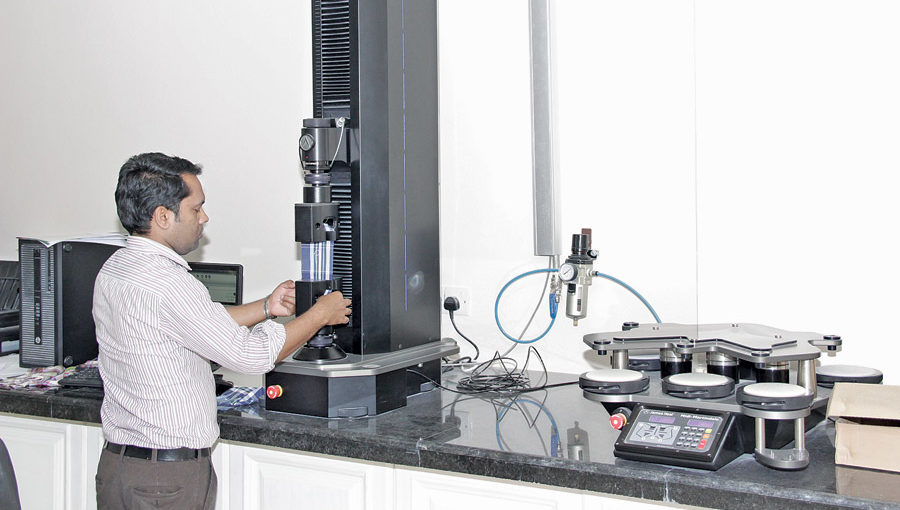
The loom utilizes less air for weft insertion due to an improved air stream angle and the optimized shape of the reed’s tunnel allows the sub-nozzle to be located closer to the reed, thereby preventing the air stream from scattering. The company has also installed a heat recovery system capable of saving US $ 5,100, 500,000 litres of water, 40,500 cubic metres of natural gas and even reducing the carbon emission by 60+ tonnes annually. Paradoxically, the heat recovery system which can save so much costs US $ 3,000 only. “We would have a certain edge over other textile companies in terms of efficient utilization of resources because all the machines and technologies were bought with an idea to have energy and water efficiency at the centre,” points out Raashid Ashraf Khan, CEO of Silver Composite Textile Mills, who was recruited specifically to give shape to Salim’s monumental expansion plans. The company has a fabric and yarn testing lab with all the equipment from the UK-based James Heal and only companies such as Arvind have such a lab.
At full capacity, the garmenting unit will have four floors, each having 16 lines with 58 sewing machines in every line, but as of now only one floor is operational. Focused at manufacturing dress shirts, the setup has 800+ sewing machines from Juki, finishing equipment from Veit and spreader from Gerber.
The fabric plant has been set up in the same premises that house the spinning unit and where the new garmenting facility for making dress shirts, which is the most recent investment of the Silver Line Group, is coming up. At full capacity the garmenting unit will have four floors, each having 16 lines with 58 sewing machines in each line, but as of now only one floor is operational. Focused at manufacturing dress shirts, the setup has 800+ sewing machines from Juki, finishing equipment from Veit and spreader from Gerber. Highlight of the company’s shirt manufacturing operations is the unique inline material movement system devised by Nihal Ratnayake, Consultant, Silver Composite Textile Mills (Garmenting Division), who is working towards reducing the number of machines per line from 58 to 47.
The company started with the conventional single long sewing lines with feeding from the front and output at the end. In the next phase, the lines were divided into two parts with newly created lines facing opposite directions and the in-line material flows in U-shape. In the present layout, the lines have again been divided as part preparation lines and final assembly lines but each part preparation line is placed adjacent to the final assembly area where that same part is being attached to the final garment. Hence the in-line material flow is lateral which means that pieces are passed on through side-ways direction to the adjacent sewing line; for example, pocket preparation is being done in a separate line but is adjacent to the pocket attachment operations. “With such a feeding system, we have been able to reduce the transportation time further, hence reducing the throughput time and increasing the output of every line,” explains Nihal, who also has plans to convert the centralized finishing department to an end of the line finishing system and allocate one finishing line to handle the output of 5-6 sewing lines. One small finishing production line will however be kept to handle urgent styles.