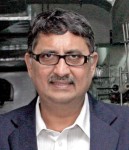
After Tirupur and Ludhiana, the Delhi-NCR region is considered the next major hub for circular knitted fabric. Many garment exporters like Gupta Exim, V&S, SPL, Celestial, among others have in-house knitting facilities for captive consumption and also for supply to other garment exporters. However, many other garment exporters like Shahi, Orient Craft, Richa & Co. to mention few and having in-house knitting machines still outsources knitted fabric from job workers. Some leading knitted fabric manufacturers in Delhi-NCR region like Durga Fabrics, Mercury Fabrics, Shyamtex, Hotz Industries among others, are either producing greige fabric or selling processed fabric. Team Apparel Online brings an update on the knitted fabric and garment industry flourishing in the Delhi-NCR region.
The good news for Delhi-NCR is that the demand for knitted garments is on the rise, the general consensus is that the market has really picked up this year and companies like Orient Craft and Richa, to mention some are almost doubling their capacities in knitted garments. Though the knitting industry is booming, still there are certain areas which need concerted attention, and the most important one is processing. “In India, dyeing and processing is still a weak link, and while processing of woven fabrics in the big mills is good, problems still exist in knitted segments. China has always been strong in processing and if we compare ourselves with Bangladesh in knitted fabrics, they have really gone ahead of us. The hand feel of their fabric is so soft and smooth and the drape is wonderful. No matter how good our greige fabric may be, our processing capabilities cannot give the desired result,” says Mahesh Mundra, CEO, Jayshree International, a Noida based vertically integrated company, doing a turnover of over Rs. 300 crore through its yarn trading, manufacturing of woven fabrics and knitted and woven garments.
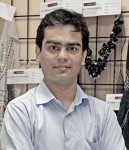
Spelling out his views as a manufacturer of knitted garments, Parag Agarwal, CEO, Nath Brothers Exim International Ltd. avers, “Undoubtedly processing is a huge problem in knitted fabrics. We have to do a lot of engineering in-house to use these fabrics as the shrinkage levels are very high and unlevelled dyeing is a regular problem.”
To overcome the problems of quality and delivery times, V&S International went in for backward integration with knitting and dyeing facility about 12 years back and since then there has been no looking back. Established in 1992 by C.P. Gauba as a garment export company, V&S initiated the integrated unit in 2001 with the capacity of 5 tonnes per day and has successfully implemented two expansion programs since then to bring up its production level to 20 tonnes per day. “Due to our in-house knitting facility, knitted garments have become our strength and today 70% of our business comes from knits, while the remaining is accounted for by woven garments,” claims Sahil Gauba, Director, V&S International according to whom if quality and timely deliveries are in place, there can never be dearth of business.
[bleft]“We have to do a lot of engineering in-house to use these fabrics as the shrinkage levels are very high and unlevelled dyeing is a regular problem.” Parag Agarwal, CEO, Nath Brothers Exim International Ltd.[/bleft]
Realising the shortage of quality knitted fabric in Delhi-NCR region Babbu Sachdeva, Managing Director, Mercury Fabrics who started his career as a knitted fabric trader, felt that there was tremendous scope of improvement in both the fabric variety and quality, which prompted him to setup a very modern knitted fabric manufacturing facility. With almost 30 circular machines, Mercury is a fully automated state-of-the art production unit at Bawal (Delhi-Jaipur highway) with complete modern in-house processing facilities to manufacture very fine knitted fabric for high-end ladies wear. “We give special performance finishes such as Gold, Silicon, Moisture Wicking, Anti-Microbial, Perfume and UV Protection finish, etc.,” shares Sachdeva.
Amit Aneja, a well known textile consultant and former Regional Fabric Head at JCPenney’s India Office while talking about Mercury Fabrics says, “If you talk of basics, 100% cotton single jersey, then Mercury has a lot of competitors but in viscose lycra or poly viscose lycra there are a very few competitors for them. The kind of quality they give is amazing. The shrinkage control and heat setting of the fabric that Mercury gives, I don’t think that many companies can offer.”
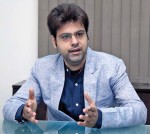
The next stage of expansion for Mercury would be knitting of printed spandex fabrics which have huge demand in the international market, but great dearth of quality suppliers in India. “There are very few knit manufacturers in India, barring a few in Ahmedabad who can handle printed knits, so the exporters are importing the same from China. We intend to add printing facility very soon to offer our customers with a full range of pigment, reactive and disperse knits printing,” informs Sachdeva.
Corroborating Sachdeva’s views, Sanjeev Garg, CEO, Genus Apparels, Faridabad says, “In Delhi-NCR region there is no one who can offer prints on knits; rotary printing is absent in this region and we have to get it done from Ahmedabad, which is why we have a team in Ahmedabad to coordinate our demand for printing on knitted fabrics. Many reasons are cited for the absence of printing in the region from the environment conditions to the properties of water, absence of technicians and other miscellaneous factors which act as a hindrance to quality printing on knits.”
Dependence on Job Workers
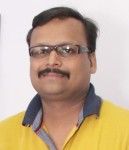
Interestingly, a majority of the garment exporters who have their own in-house knitting facility still have to depend on job workers for fabric as their capacities are limited both in terms of volumes as well as variety in designs. Noida based Durga Fabrics with 80 knitting machines, is knitting fabrics for almost all big garment exporters in Delhi-NCR region. Established at the turn of the century in 2000 by two brothers Sanjay and Vinod Garg with 3 knitting machines, the company is producing unprocessed fabrics, both greige and yarn dyed, for fashion garments and sportswear along with fabric used for medical purposes. “In 95% cases the garment manufacturers provide us yarns. We produce 100% cotton, PCs and other blends which a garment manufacturer may ask for. We mostly knit as per the design given by the exporters,” states Sanjay, a B-Tech in Textiles. The company is equipped with machines which can knit fabric with any amount of blends and stretch. “We can give stretch level up to 200% and produce fabrics from 40 GSM to 1000 GSM,” adds Sanjay who agrees that the knitting industry in India is very unorganized and so is the processing of knits.
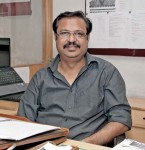
The job workers prefer to stick to their knitting job and do not get into procurement of yarns nor offering designs. As per Sanjay, though they do their own developments but it doesn’t really work out as it becomes a long drawn process. “Whatever we develop, takes almost a year to reach the buyer; first we send it to the exporter, if he likes it he will make samples out of it and then send it to the buying office; again if the buying house likes it then they will send it to the international buyer, who will put it in his showroom for a three months to test the market, after which he will give his colours or fibre preference to the buying office – the whole process is very time-consuming, so it’s better not to get into it,” argues Sanjay who is now planning to go for backward integration by putting up an air-jet spinning plant in Neemrana which is 20 times more efficient than spindles. “Twenty spindles are equivalent to one air-jet. Investment would be around Rs. 30 crore and the plant would be commissioned by next year in December. With our own spinning we will be able to offer the unprocessed fabric at cheaper rates and better quality,” adds Sanjay who is also looking at putting up a processing house after the commissioning of the spinning unit.
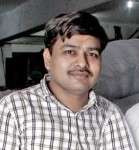
Order Flexibility
In knitted fabrics there is no MOQ (Minimum Order Quantity) system. From a sampling order of 5 to 10 kgs, the order can go up to 1000 to 2000 kgs. Smaller the quantity, higher is the price. As order to order varies, in majority of the cases, the fabrics in stocks are not of any use for the garment exporters. They get the fabric developed as per their buyer’s specification. “We don’t take anything from the ready stocks with the knitters as we are not doing run-of-the-mill kind of stuff and most of the time we are doing qualities which are not very basic qualities. Every order of ours is a new development and our quantities are not very large so the costs are higher, but then our surface ornamentation is so much that we derive our margins from there,” avers Parag.