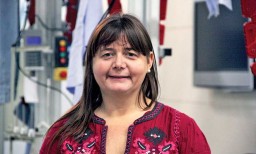
With over 4000 systems installed in more than 60 different countries, the Eton Systems concept of a unit hanger system has been widely accepted and recognized as a global manufacturing standard. The company holds a coveted stature as a solution provider for different production areas, such as apparel, home textiles, furniture, and the automotive industries.
Founded by Inge Davidson in 1967, the Swedish company Eton Systems AB arose from the shirt manufacturer Eton Fashion, a well-regarded company making shirts since 1928. While working as the Production Manager in the family-run shirt factory, Davidson discovered that 80% of the shirt manufacturing time was non-productive because of the inefficiencies related to the bundle system that dominated the sewing industry then. Thus, arose the idea of the world’s first Unit Production System (UPS) and Eton Systems was born.
With the aim to address unproductive handling, long lead times and ergonomics-related issues, Davidson designed an ingenious hanging conveyor system that automatically moved hanging garments between different sewing operations and wasted no valuable floor space nor required a major modification to existing machines. The system was conceptualized as a “mechanical hand” holding the garment during sewing and was made possible after two years of rigorous hardware development and testing. The birth of the Eton Systems thus revolutionized the garment production.
Davidson’s system was simple, effective and brilliant. It allowed all the materials needed for a specific garment to be transported as a unit directly to the correct sewing station. When the operation was completed at one workstation, the system would automatically pass it on to the next workstation. The productivity increased immediately as operators could now concentrate on sewing, without wasting time, handling bundles of unfinished materials. In addition to increased efficiency, the production could also be planned and controlled down to the finest detail. Davidson was thinking of Lean production before the term even existed.
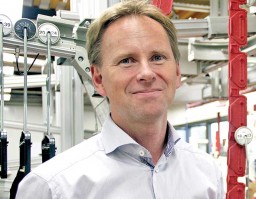
With time, the Eton Systems remained the same in principle, yet it has continuously evolved and refined itself. One significant expansion of the system is the Eton Systems software, the EtonSelect, which has been developed in-house. Customer’s feedback also has been a strong factor in the evolution of Eton Systems. “The manufacturer’s production data is very important part for us when creating the best possible solutions for our clients,” says Lars Kry, Eton Systems R&D Manager, predicting that the software will become more and more integrated with Eton Systems client’s ERP Systems. And this exchange of information will make the system fully adjustable to the needs of the client.
[bleft]“The manufacturer’s production data is a very important part for us when creating the best possible solutions for our clients as this exchange of information will make the system fully transparent.” – Lars Kry R&D Manager, Eton Systems[/bleft]
Since Inge Davidson passed away in 2011, the company is being run by Tintin Jonasson as the CEO, in the same spirit as her father, aiming to develop his innovation even more. “We want to always be at the forefront of UPS technology, giving smart solutions to our customers, helping them to be world class manufacturers,” says Tintin Jonasson. “It is a partnership where we want our customers to get the most out of our knowledge, which includes so much more than just making production systems that offer increased efficiency and profitability. We aim to create an ergonomic work environment for the employees, since we believe that a healthy work place is vital for a long-term economic prospect.”