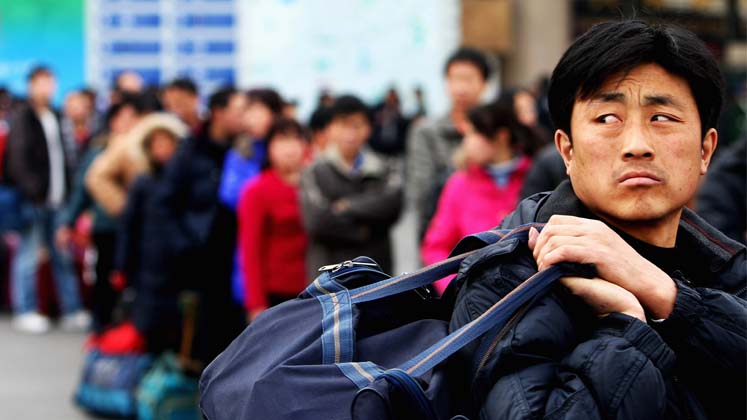
The very reason that made China a manufacturing heaven in the first place – abundance of cheap labour – is threatened today! Reports from Chinese Ministry of Human Resources and Social Security claim that China today is in a precarious position with labour shortage in 36 manufacturing-related positions out of 100 diverse positions. The report also claims that the number of open positions for occupations on the rankings jumped to 1.418 million in Q4, which is up by about 100,000 from 1.316 million seen in Q3. That says it all!
This implies that leading factory owners across China are struggling to get labour force – forget about hiring skilled workers. One also cannot overlook the fact that the pool of workers available to the manufacturing industry has been dwindling over the years. This is not only because jobs in other industries have become lucrative but it is also because of the impact of the legacy of decades of one-child policy that was officially scrapped in 2016. Notably, as per official figures, China’s working age population has gone down by more than 5 million people in the last decade as births have slumped, and this is despite a rollback of the one-child policy.
Migrant workers are uneasy to come back…
To make it worse, the migrant workers on whom the entire manufacturing industry survives and thrives are still worried of getting infected by Coronavirus despite the low number of cases in the country, and this worry is forcing them to stay at homes, thereby hitting the businesses in the country significantly. Chinese migrants who had returned to their hometowns for the Spring Festival are reluctant to come back to cities and according to a reported survey conducted in the country, women migrant workers are less likely than men migrant workers to return to factories.
The report also highlighted that having a preschool-age kid had a negative impact on women migrants’ employment decisions. Notably, Covid-19 has today reinforced traditional gender roles in many apparel and business establishments in the country, and intensified labour market inequalities. Also, the recent floods in many parts of China haven’t helped the cause either. In fact, as on March 2021, the Statistics Bureau said that there were still 2.46 million fewer migrant workers than during the same period back in 2019.
Several migrant workers have been battling tough working conditions, employed as labourers in garment factories or as courier employees in China’s e-commerce firms. Also, a stringent residency system — called ‘hukou’ — prevented migrants from accessing public health care and schools, or buying property in their city of work. In such a scenario that’s already plagued by high living costs, migrant workers are not keen to rush to cities – at least for the time being.
Chinese youth is no longer interested to work in apparel factories
It is getting tougher for garment factory owners with each passing day. Particularly, small garment factories, which have relatively harsh working conditions, have lost their attraction to young workers, says Yang Zhixiong, Executive General Manager of the Guangzhou International Textile Trade Zone. There is nothing more disheartening than seeing young men and women running away from apparel units. Yang adds, “Youth would like to try more challenging jobs, especially in the creative design and automated industries.”
However, it is not only small apparel units in Guangzhou that are facing the so-called ‘labour pain’. Several large business establishments in Guangdong’s Pearl River Delta region are also desperately looking for more workers. Ever since the Spring festival ended, it’s not been a good time for factories in the region. One has seen employers from garment factories queuing up in Datang (suburb of Guangzhou), one of south China’s major textile hubs, to recruit garment workers. The sad part was that despite holding placards offering variety of job positions and competitive salaries, the recruiters still couldn’t hire enough workers to meet the growing business demand.
The salary may appear attractive for some outsiders, but insiders are still cautious. Given that workers are paid by the piece, higher salary would mean taking up heavy workloads. In fact, many workers said that they may have to work for more than 14 hours a day for that salary. Also, the labour-intensive job requires doing repetitive work in the same position – not to mention the occasional risks to a worker’s health.
Also Read: It’s official! Apparel sourcing from China is down as says US import data of H1 ’21
Income instability is a worry too…
Now, even if workers get handsome salaries, the unstable income is a constant worry for them. Those desperately seeking for jobs say that initially salary may be high, but it will definitely be cut, as and when more workers come in. Also, as most of them are non-permanent workers, and wages are paid on the basis of the number of pieces finished, the price for each piece floats. While some may be lucky to make over 10,000 yuan in a month, many others may struggle to make even 5,000 yuan.
In such a scenario, many workers are not keen to work in garment or textile units, where one’s salary fluctuates so significantly. Besides, there are lots of opportunities for gig work livestream e-commerce hosts, key opinion leaders, better known as KOLs, or ‘wanghong’, delivery men, as well as online-hailing taxi drivers. So, with several job options available in the market, not many opt for an exhausting factory job that also doesn’t offer a stable income.
Measures to combat the ongoing crisis; technology is the way going forward
To battle the ongoing labour shortage crisis, human resource officials in Shenzhen, Guangzhou, Dongguan, Foshan, Huizhou and Zhongshan are closely collaborating with their counterparts in the provinces of Yunnan, Sichuan, Guizhou, Hubei, Hunan and Jiangxi and the Guangxi Zhuang autonomous regions to conduct over 180 online job events that are offering more than 460,000 jobs.
In fact, by March 2021, provincial authorities said that over 2,000 chartered buses, 10 chartered trains as well as 10 chartered flights had been organised to send over 86,000 workers to companies in the six cities, wherein there was a surging demand for migrant workers. But the moot question is how consistently the authorities and the Government can keep on taking such initiatives. A worker will have to be tempted, in these trying circumstances, to come back to apparel or any manufacturing unit.
Besides, many garment units in the country are gradually opting for technology upgradation. For several factories that have been consistently driving much of modern China’s growth, the shortage of labour is pushing the wages up. Consequently, while some firms are relocating, quite a few are investing in enhancing automation. It seems distinct now that the future depends only on technology upgrading in manufacturing industries, and if it is not done at the earliest, then the factories, especially small-scaled labour-intensive textile firms, could be in for some major losses.
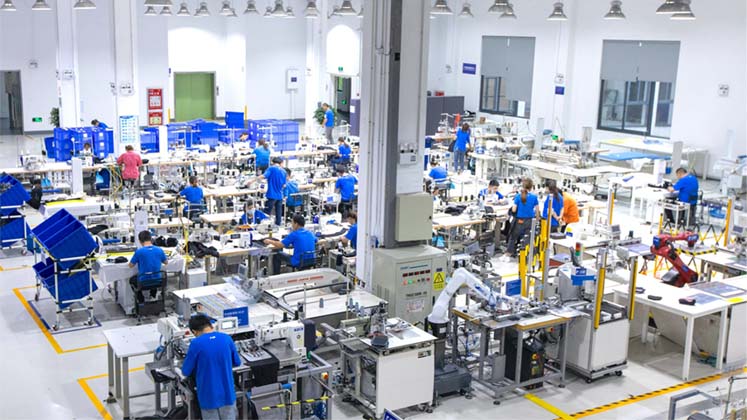
Another strategy that may work is the new three-child policy of the Chinese government. The immediate effect of the three-child policy is expected to be positive, though at a smaller level. If we assume that around 6.5 per cent of couples in the 25-49 age group have three children, then one may see a total increase of 6.68 per cent in terms of birth rate – and if that happens then the labour force gap may come down by 7.15 million with a gap remaining of 4.65 million. But, it’s still a long way to go!
The labour shortage is here to stay for some time, but in the long-term, China must make reforms in policy areas that include health care, retirement and immigration – that’s the only way to go forward for the world’s second largest economy to combat the crisis.
Also Read: “India among high-priority sourcing partners” – QIMA report