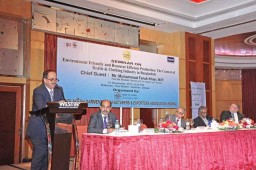
Riding on the back of Batexpo 2012, BGMEA, in association with Intertek and GIZ, organized a seminar to invoke awareness on protecting the environment and implementing safety measures at garment factories.
The well-attended seminar was chaired by Civil Aviation and Tourism Minister Faruk Khan, who very aptly emphasised the importance of upgrading the work culture of the industry to meet newer challenges. “To work sustainably in the new business environment, it is important to ensure resource efficient production and among the many measures that can be undertaken, installation of effluent treatment plants (ETPs) would go a long way to benefit the industry,” he said.
The minister added that since 70% of the production is dependent on gas energy, with very little hydro power being generated, other alternatives such as solar energy and wind mill projects should be installed in the country. “We know now that it is possible to have environment friendly power generation in the coastal cities like Chittagong and I am very hopeful that some windmill projects would be operational in the next six months,” informed the minister. He also pointed out to the dire need of having safety norms in place to avoid fire incidents like the one that shook the industry recently.
[bleft]“Textile sludge, a residue of waste water treatment in washing/dyeing and finishing plants of the garment industry, poses an environmental problem due to volume and hazardous substances. Lack of rules and regulations, know-how, awareness, and buyers’ pressure for solution has led to cooperation between GIZ and DoE/Ministry of Environment for drafting standards and guidelines for the management of textile sludge..”
“IFC program on cleaner production for Bangladesh textile sector is to minimize resources used in textile processing by raising factory-level awareness on resources efficiency and identifying/implementing low-cost measures. The company has partnered with key buyers like Levis, Kappahal, Lindex, Mothercare, Tesco, WE Fashions, Primark, New Look and G-Star.” [/bleft]
The panelists expressed concern on the depleting natural resources. Shafiul Islam, President BGMEA was particularly distressed over reducing water levels of the country. He urged the industry to take measures to conserve water and the environment. “Bangladesh is one of the most vulnerable countries in the world due to its natural geographical positioning and erratic climatic changes. The national disasters that have hit the country over the decade account for over 1.5% of the total such disasters which have hit the world, which is alarming for a small country like Bangladesh,” said Islam.
Underlining the fact that factories which have introduced cleaner production techniques have succeeded in enhancing output even with lesser resources, Naureen Chowdhury, Associate Operations Officer of IFC-SEDF said, “Cleaner production techniques can save about US $ 150 million each year for the industry.” SEDF facilitates the growth of small and medium enterprises by helping improve their access to finance through a supportive financial infrastructure and helping businesses adapt to the impacts of climate change.
Appreciative of the efforts of BGMEA to educate the industry with topical seminars, Dilip Gianchandani, Regional Director, Intertek stressed the importance of collective effort to become a sustainable supply chain. “By thinking green, acting green and going green, the industry can effectively save resources in the production system. We can have collaborative all stakeholder engagements, which means the entire supply chain is collectively managing renewable and scarce resource of water and energy. Unless we make efforts in these directions, we won’t be able to achieve anything…as said, “If you cannot measure, you cannot manage,” said Dilip.
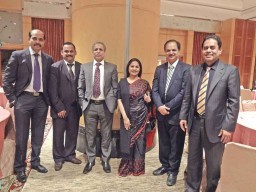
He went on to highlight the many initiatives Intertek has undertaken in the direction of special certification programs through which they are providing effective production systems so that one can measure energy and save resources. “We have a certification program called “Think Green Initiative” in which we provide ways of auditing the processes, measuring resources and making it possible to go for greener and cleaner production,” informed Dilip who also congratulated GIZ for supporting all green initiatives for efficient production systems and energy saving.
Md. Ashraful Hassan, Managing Director, Grameen Knitwear Ltd. highlighted that the textile industry is the second largest water consuming sector in the world after irrigation, as generally 80-100 litres of water is required to dye 1kg of fabric. “Today, almost all the dyeing houses in Bangladesh attached to over 5,400 factories are using underground water, the reducing levels of which is already a matter of grave concern, hence there is an urgent need to adopt technologies which reduces water consumption, and go for green factories with open space and maximum usage of sunlight,” said Hassan.
GIZ is a German organization working in Bangladesh to support green production, green factories, waste water management and train the workers in these areas. It offers demand-driven, tailor-made and effective services for sustainable development. “We have taken upon a project where we will train the women workers for the middle management level. They will be trained on issues like waste water management, energy saving and chemical management,” informed Magnus Schmid, Program Coordinator, GIZ. The organization is also looking at taking projects like green industrial park and green factories for the RMG sector in 2013.
Urging the garment unit owners to economically use water and energy, Dr. Ainun Nishat, Vice-Chancellor of BRAC University and a well-known environmentalist warned the industry that buyers would move out to other countries if the Bangladesh industry falls short in complying with global standards. Classifying apparel industry as the spine of national economy, Dr Nishat said, “The apparel unit owners should act positively to make all units in the sector environment-friendly by fixing their own standards rather than waiting for global pressure to set the same. The solutions are dwelling within the country and also there are global organizations which are ready to help RMG unit owners achieve the targets.” He also stated that the majority of garment units lack proper structure and design, which is the root cause of frequent fire incidences endangering the lives of workers.