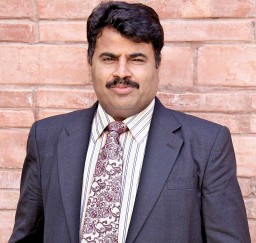
Country Head, EPIC Group, Bangladesh
Awarded with the prestigious LEED Certification in 2011 by the US Green Building Council and verified by the Green Building Certification Institute (GBCI), the Epic Group’s CIPL Project in Dhaka is the first LEED Certified project for the Group and also the first LEED Certified project in Bangladesh. The state-of-the-art air- conditioned factory, spread in an area of over 5,00,000 sq. ft. for garment manufacturing and finishing, boasts of in-house wet and dry processing, embroidery, printing, and a dedicated wrinkle-free post-cure facility. The interesting feature of the achievement is that the factory was not built as a Green factory, but strategically converted into a Green factory after five years of its establishment with an investment of around US $ 3 million spread over the last few years.
Cosmopolitan Industries Pvt. Ltd. (CIPL), a company of the Epic Group, achieved LEED certification for optimizing the use of energy, lighting, water and material as well as incorporating a variety of sustainable strategies including Green design and construction features, sustainable material purchases, and healthy indoor working environment for occupants. The company has very intelligently used its assets to cut down on wastages and thus saving critical resources. To generate steam no diesel is required, instead exhaust from the gensets go to the boiler for generating steam. “When you run the turbine, approximately 360°C exhaust combustion is generated, which is captured and passed through a chamber into a boiler to generate steam. By channelizing the exhaust in this way the exhaust temperature comes down by 100-120°C, reducing the in-house impact by nearly 100°C,” informs Virender Goyal, Managing Director & Country Head, EPIC Group, Bangladesh. These heat recovery boilers cost US $ 87,000, while per year saving according to the company is US $ 99,000.
Not just that, but the boilers are linked online with a computer to monitor how much gas is being consumed and what is the efficiency. In a typical boiler, as a routine after every 12 hours water is thrown out because of the hardness created and refilled with fresh water. But at CIPL, since the boiler is monitored online, the water is replaced only when the hardness level is achieved. “If we save even one ‘blow down’ in two days, we save $ 10,000 in a year and also three tonnes of water,” says Goyal. The plant has its own RO plant for in-house water treatment. “At most washing plants, the liquor ratio is 1:10 or 1:12, but we have 1:3 or 1:4, so if your water consumption is less, your steam consumption is also less and your chemical consumption too is less; therefore, everything automatically comes down,” reasons Goyal. He informs that by maintaining a low liquor ratio the unit has saved 1.25 million litres of water till date, which is equal to the daily drinking requirement of 2,00,000 persons.
Denim wash for one pair of jeans consumes around 3500 litres of water and 400 mega joules of energy, and to optimize consumption, CIPL is using new enzymes which can work in cold temperature and are bio-degradable, to save energy and also because when the water/enzymes go into the ETP, we do not need a chemical to degrade it. The company has also installed a hot water mechanism to directly provide hot water in washing, saving 20 minutes in raising the temperature to the desired level.
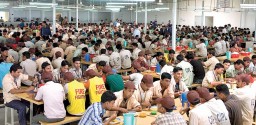
In the normal process, when you take any steam and put it into normal water, the temperature of the steam goes down from 200-250°C to 100°C, and in this transition lot of energy is wasted. In the system we are using energy which is going waste, and recycling it into steam resulting in energy conservation of almost 50%. “The investment in this hot water mechanism is around US $ 20,000 and the ROI is just 8 to 9 months,” says Goyal. The company claims they are saving US $ 24,000 annually by using the hot water mechanism.
Contrary to popular perception, the company believes that going Green is not adding cost; in fact it is primarily about saving energy and cost. “Being Green also means that you are cost-effective, because if you consume fewer resources, you can be sustainable for a longer period of time. This is the fundamental of business,” avers Goyal. Saving cost can be seen at many places including the air circulation system to keep the factory cool, ensuring that no gasses are being used for air conditioning.
[bleft]A lot of energy is wasted in the normal process to bring down the temperature of the steam from 200-250°C to 100°C, in washing denim. But with the use of hot water mechanism, the temperature is reduced much faster and the energy which is going waste is recycled into steam resulting in energy conservation of almost 50%. The investment is around US $ 20,000 and the ROI is just 8 to 9 months.
By maintaining low liquor ratio in dyeing the unit saves hugely not only on water, but also in steam generation and electricity. Epic, working with a liquor ratio of 1:3 or 1:4, has saved 1.25 million litres of water till date, which is equal to the daily drinking requirement of 2,00,000 persons.
Denim wash for one pair of jeans consumes around 3500 litres of water and 400 mega joules of energy, by using new enzymes which can work in cold temperature and are bio-degradable, there is saving on energy and also on chemicals because when the water/enzymes go into the ETP, we do not need a chemical to degrade it.[/bleft]
Another area of operation where energy is being saved is in the wrinkle-free finishing process. A special spray was developed in India which creates mist inside the spray drum and because of this mist 1 kg of garment when applied with 200 ml of chemical, will weigh 1.2 kg, not even wasting 10 gm of water or chemical. “I don’t think anybody else has this spray. Even the residual mist gets condensed, and recycled, and the process continues until all of it is utilized,” says Goyal.
Besides use of technology, policies and structures have been put in place to monitor critical parameters and set targets for the next year. Even to the extent of smallest of the details such as how many cartons are recycled and how many cartons will be needed from virgin paper. “Some buyers insist on virgin paper cartons, but we motivate them to buy the recycled ones. We keep a record of how much paper has been recycled to manufacture the paper from which these cartons are made. That is how we decide our targets, like this year we used 70% of recycled cartons, next year we would be using 80%,” reasons Goyal. He is confident that the utility cost of the factory in garment manufacturing is the lowest in Asia, because it is based on strong fundamentals of cost savings.
The ISO 50001:2011 certified factory (for energy conservation) monitors carbon emissions on a daily bases. The company studies the trends emerging from the data and identifies the parameters that they need to work upon. The company even records the time and distances the garment travels, right from cotton picking to retail shelves to calculate the carbon emission with a target to reduce this emission. “We have gone in for a project with Levis – ‘Cleaner production’ – with the aim to minimize carbon emission in the complete production cycle,” informs Goyal.
Being the first Green factory in Bangladesh the responsibility to set benchmarks is well understood. “First we had to build the correlation and index, even the auditors didn’t know because it was a new company for them. It took my 30 years analytical skills to establish those standards. There are two things: Green building and Green factory. Green building means that you have taken care of lightening, direction, air conditioning, etc. But when you say Green factory the process comes into the picture, which is a challenge, but we have a detailed checklist for maintenance and the successful implementaton is for all to see,” concludes Goyal.