The quality of any apparel is not only about the perfection of sewing but is also closely related to the products that go into making the apparel, fabric being one of the main components. Analysing fabric quality is a technical process and is evaluated by a 4-point inspection system, popularly expressed as points per hundred square yards (PPHSY). In common interpretation, lower PPHSY means better quality fabric. Interestingly, the acceptable quality of fabric is not standardised and each buyersets different acceptable maximum unit points per 100 sq. yard for their fabrics based on their customer profile. A case in point is that while BUYER 1 requires that a single roll of a fabric cannot exceed 20 points per hundred square yard, BUYER 2, on the other hand allows only 18 points. There are two different requirements such as PPHSY/Roll and PPHSY/lot. For example, for BUYER 1, PPHSY/roll may be 20, and PPHSY/lot is 15. If total 20 rolls of fabrics are shipped to an apparel manufacturing unit, average PPHSY for these 20 rolls can never be more than 15.
Should manufacturers be happy if a buyer allows higher defect points? What is the relation between Fabric Defects, 4-Point Inspection and Defective Panels?Nazmul Hassan, Senior Executive, Quality Assurance, Envoy Textiles Limited, Bangladesh and Prabir Jana, Shahi Chair Professor Industry 4.0, National Institute of Fashion Technology, India discuss the missing link, which is critical for every manufacturer.
With increase in customer awareness, demand for quality fabric is increasing and now customers are more concerned about the quality of the material. In order to fulfil demand of quality material, it is importance to avoid fabric defects, for which generally 100 per cent of the fabrics manufactured are inspected for defects. There are various fabric inspection system used in apparel industry – 4-point inspection system, 10-point system, Graniteville ‘78’ system and Dallas system. Out of these,4-point inspection is most popular in the apparel manufacturing industry.
What is 4-point inspection?
The 4-Point System assigns 1, 2, 3 and 4 penalty points according to the size, quality, and significance of the defect. No more than 4 penalty points are assigned for any single flaw. A defect can be measured either in length or width direction; the system remains the same. Only major errors are considered. No penalty points are assigned to minor defects. A major defect is any defect that would cause a final garment to be considered a second. Whenever errors are recognised during fabric inspection under 4-points ystem, the defect must be assigned a number of points depending on the severity or length.
INCHES ( ˝ ) | (MM) | POINTS |
From 0 > 3″ length/width | Up to 75mm | 1 point |
From 3.1″ > 6″ length/width | 75mm > 150mm | 2 points |
From 6.1″ > 9″ length/width | 150mm > 230mm | 3 points |
More than 9″ length/width | More than 230mm | 4 points |
Upon the number and the size of the imperfections in the given yard, a maximum of 4 points can be given to one linear yard.Four points can be given for each linear yard when a defect is running continuously along the length of the fabric. So, maximum point that can be assigned to any fabric is 400 PPHSY. Generally, there are no benchmarks for acceptable standards, however less than 40 PPHSY is considered good fabric. In a contract manufacturing scenario (especially CM) where garment manufacturers procure fabric from nominated fabric supplier, the buyer/retailer/brand decides the benchmark PPHSY that can be accepted.
Defective Panels and the Manufacturing Challenge
After the fabric is spread and cut, the garment manufacturer replaces the defective panels with defect-free panels, cut from the end-bits of each roll. In a CM scenario, buyer does not allow additional meterage once a fabric within acceptable ‘defect points’is given. But the question that is most relevant here is whether this is a fair deal.Taking the example of BUYER 1, which sets a maximum PPHSY of 25, does it ensure manufacturers will be able to replace all the defective panels with available end-bits? If not, from which source will the garment manufacturers manage additional fabric to cut again to replace the defective panels? The nominated fabric supplier will not provide further fabrics free of cost as its fabric meets the buyer requirement.
If there is a known relation between PPHSY and the number of defective panels, then the job would be easier for buyer as well as manufacturer. Today we don’t have any known theory or formulae to predict how many defective panels will be generated based on defect points and/or what types of defects contribute more to the defect points?
Practical application of 4-point inspection system
Taking the case of a fabric roll of 120 metre length and 45 inches width, and when inspected the following defects are found:
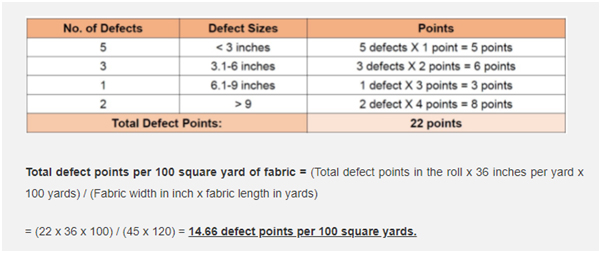
Now the 120 metre roll has
- Total numbers of defects = 11 (sum of first column)
- Total defect points = 22 (as per four point inspection)
- PPHSY = 14.66
Suppose we spread this fabric roll in 12 layers of 10 metre lay. After the cutting is over, we check for defective cut panels. What are the theoretical possibilities?
- There are a total 11 defects in the roll, so a maximum 11 cut panels should be defective, if we assume one defect is restricted within one panel.
- The number of defective panels can be less than 11 if some defects will fall in the dead area of the marker or more than one defects appear in one panel.
- The number of defective panels can be more than 11 if any single defect spreads across more than one panel (specially for the larger size of defects).
In summary, we have no idea how many defective panels will be generated.
Please note, the buyer generally mentions the acceptable fabric by PPHSY and not by ‘number of defects’, whereas the number of defective panels are factor of ‘number of defects’. Suppose another second roll of exact same length (120 metre) has a total 18 defects and all are <3 inches. Therefore the ‘defect points’ for that roll will be 18.
Now you have two rolls of 120 metres – first with 11 defects and 22 ‘defect points’ and PPHSY of 14.66 and a second roll with 18 defects and with 18 ‘defect points’ and PPHSY of 12. Although the second roll mayappear to be of better quality than the first one, but it is likely to generate more defective panels, thus higher loss to the company.
There also exists a practice of benchmark panel rejection percentage. When panel rejection exceeds 1 per cent for fabric faults, usually the garment manufacturers claim for additional fabrics free of charge. However, panel size may contradict such practices if the benchmark is not factored style-wise. For example, a lower panel rejection percentage in a trouser marker may be more damaging than higher panel rejection percentage in a brassiere marker.
Initial Findings
While a detailed study is required to predict the number of defective panels, our initial study points towards following conclusions.
- Faults that are scattered over large area of a fabric (in comparison to defects concentrated in small area) likely to generate a greater number of defective panels.
- If length of faults is oriented to weft-way (width-way), it may produce more rejected panels than the faults, which expand in warp-way (length-way), do.
- Size and areas of patterns are also important. Large-size patterns may take away almost all of a large size fault, which saves other panels to get rejected. However, small size patterns cannot. Further when a large panel is rejected due to fault, some small size panels can be extracted from the defect free areas of large panel. Alternatively when large panels are rejected due to fabric faults, it increases fabric wastage.