One of the key attributes in lean manufacturing is the continuous flow manufacturing system, which is expected to develop an optimally balanced production line to produce on time, defect-free products with very little waste at minimum possible production cost. Unfortunately, with very little knowledge on the utility of this tool in public domain, continuous flow systems are rarely visible in the needle trade, says Chandrark Karekatti, an industry consultant. In this article CK tries to demystify the methodology for developing continuous flow system for apparel industry.
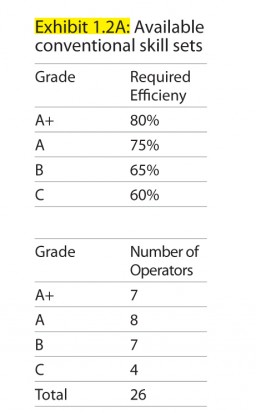
In most of the units which pride themselves of using continuous flow installations, it is nothing more than a U-shaped process layout. Another common practice observed is grouping of machines that perform processing steps in a sequence termed as a ‘cell’, however rarely seen to achieve a real continuous flow. Technically an ideal continuous flow system should enable cut panels and finished garments to flow continuously all the way from cutting to carton packing. However, this will be too elaborate an exercise for any factory to start with; it is therefore advisable to develop the flow system initially at sewing assembly operations aided with a pacemaker process to set the pace of upstream and downstream operations and intermittent supermarkets (buffer) to facilitate flow of production from upstream operations.
Even then, it is not an easy process to implement and some of the key obstacles faced by factories when moving from traditional assembly line manufacturing to flow manufacturing are:
1. Variation (product, process, schedule),
2. Machine capability (reliability and capacity),
3. Facilities tuned to produce large batch quantities,
4. Work place layout.
Since the above issues are common to most of the apparel factories, it is highly recommended to implement process enhancement tools such as 5S (visual control), Heijunka (product and process levelling), TPM (machine reliability and capacity) and SMED (style changeover performance) while implementing flow manufacturing system.
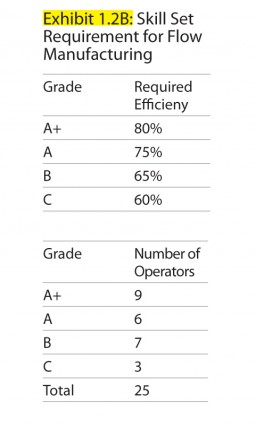
Implementing Flow Manufacturing
Flow manufacturing aims to achieve continuous production flow, where a single unit of garment flows from processes to process (bundle quantity is one). Hence it requires work centres and processes to be arranged in different configuration as compared to traditional assembly line configuration. This also requires demand dependent scheduling (pull type) as compared to traditionally practiced independent scheduling (push type). In demand depended scheduling, the production schedule is triggered by a pull signal from the customer order and this pull system links the upstream and downstream operations across the entire value stream (processes).
As an example a continuous flow system for a full sleeve shirt is demonstrated in Exhibit 1.6 made using a line plan (Exhibit 1.4) using cellular manufacturing principles against the conventional line plan (Exhibit 1.3), with an objective to achieve an efficient flow, improved efficiency and lower waste.
Steps adapted for developing flow manufacturing system:
1. Identify and schedule pacemaker process,
2. Develop work cells (work stations and equipments configured such that they facilitate flow manufacturing),
3. Develop intermittent supermarkets.
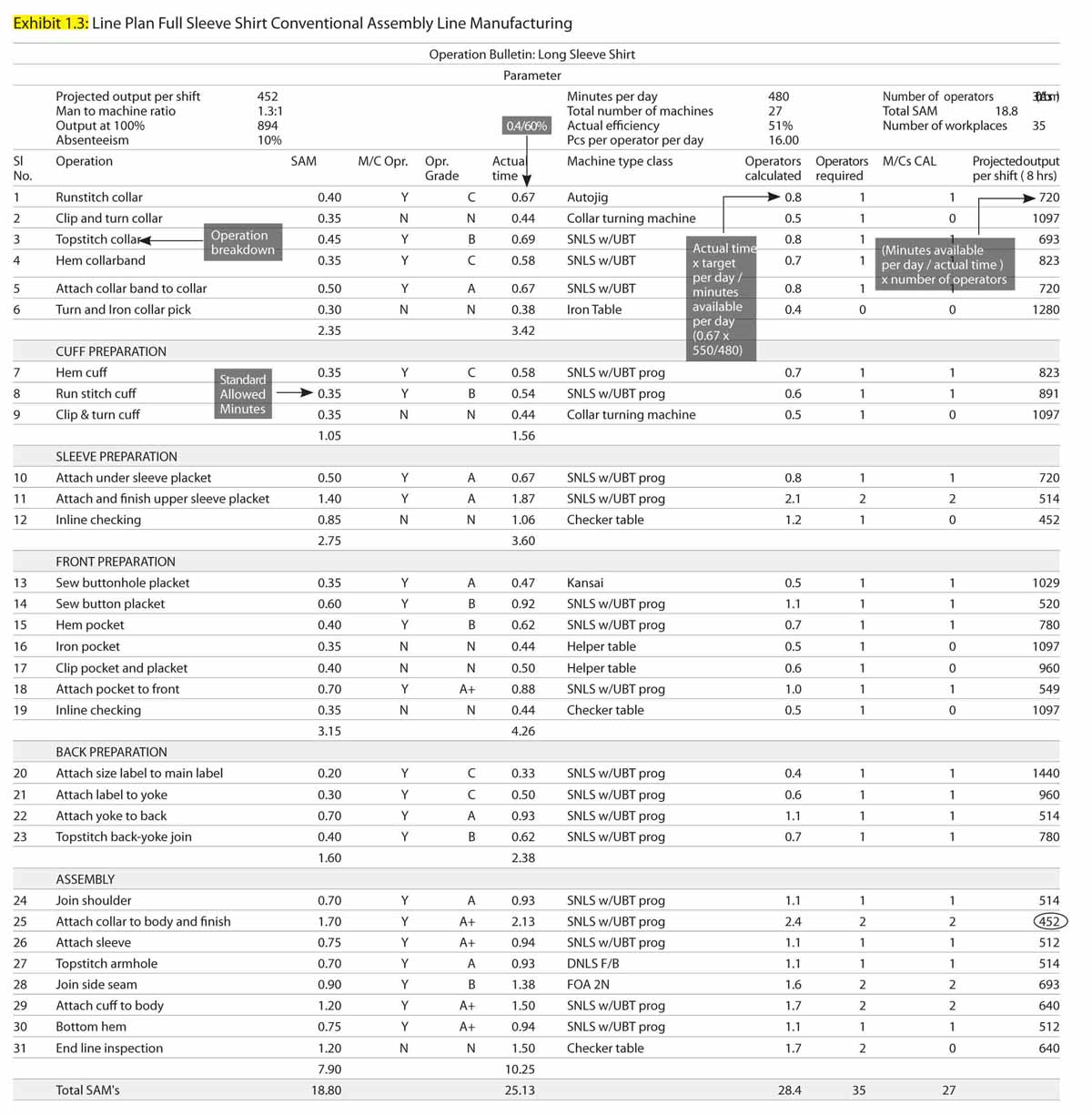
Identify and Schedule Pacemaker Process
It is important to set the pace for upstream and downstream operations in an apparel factory and cutting process set the ‘pace’ for the processes.
While the upstream operations include activities related to fabric and trim sourcing, the vertically integrated setup upstream activities also include production scheduling for fabric manufacturing and wet processing departments, whereas the downstream process include cutting room, garment manufacturing and finishing and packing. Technically the pacemaker process is identified as the most downstream process in the factory, and the way it is managed impacts all the upstream processes in the value stream. It is the point where customers order enters the apparel manufacturing value chain to control the rate of production of all upstream processes. Thus the cutting process in garment operations qualifies to be the pacemaker process, and since the way it is managed can impact all upstream operations such as sourcing and production scheduling at fabric manufacturing and wet processing departments. To convert the cutting process into a pacemaker process, the cutting process has to be scheduled to set the “pace” for all processes upstream and downstream of the value stream (Refer Exhibit 1.1). A well designed pacemaker in cutting creates a pull effect between cutting section and fabric sourcing function, thereby preventing inventory stockpiles. Here the cutting schedule (derived from master schedule) triggers the pull for sourcing and scheduling activities upstream the value stream. All downstream operations, viz. sewing, finishing and packaging work on ‘first in first out’ principle (FIFO). Thus the sewing and finishing schedule automatically conforms to master schedule (pull driven), since the cutting is triggered by master scheduled.
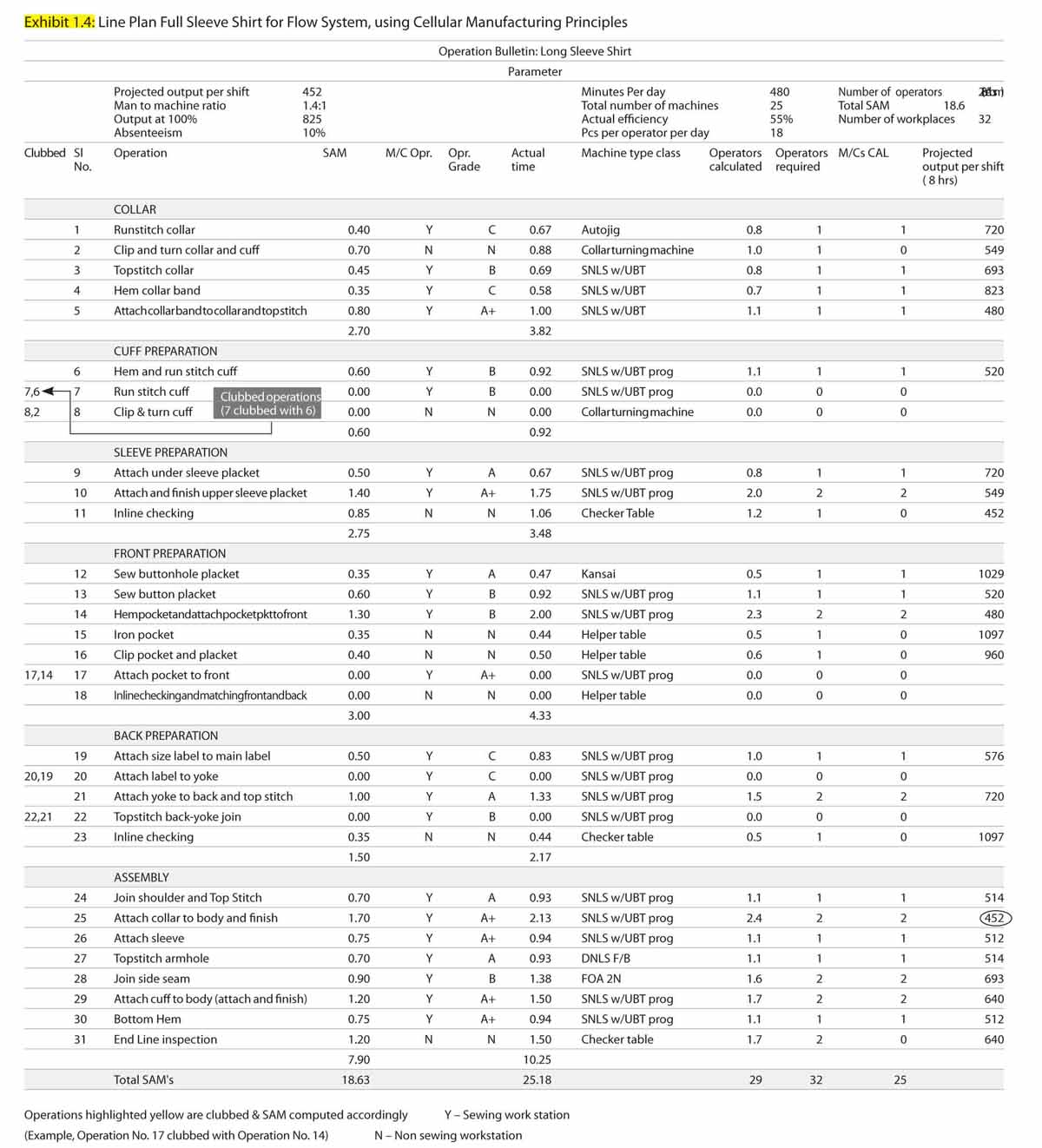
Develop Work Cells
Work cell comprises of work stations and equipments are configured in such a way that they facilitate single piece flow.
It is necessary that Industrial Engineering department develop line plan for each style that provides improved resource utilization, higher efficiency and facilitate single piece flow. An ideal configuration need not provide single piece flow on all workstations, a combination of bundle system (preparatory/sub-assembly stage) and single piece flow (final assembly stage) works satisfactorily for apparel industry. One of the pre-requisite for developing work cells are the availability of multi skilled workforce with high skill grades which facilitates clubbing/splitting of operations. The clubbing/splitting of operations also helps in developing work cells that can eliminate non value adding movements and improve resource utilization (Exhibit 1.2A shows skill set available in conventional setup, and Exhibit 1.2B shows skill set required for developing work cells), making training and skill enhancement an integral part of flow manufacturing system.
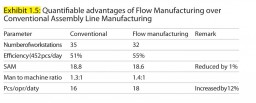
Exhibit 1.4 shows line plan and machine configuration for full sleeve shirt, developed using lean principles. Compared to conventional assembly line (Exhibit 1.3), the work cell configuration has operations clubbed and machine configuration modified (Exhibit 1.4) to achieve better resource utilization and single piece flow in final assembly (clubbed operations are highlighted yellow in separate column in the new configuration, refer Exhibit 1.4), the operation details of which has been clubbed and the configuration of the machine has been changed. Operations are clubbed to improve resource utilization and single piece flow in final assembly (Exhibit 1.6). Work centres are divided into three sections (work cells), viz. assembly, pre assembly and preparatory section.
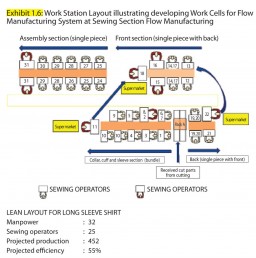
The preparatory stage comprises of collar, cuff and sleeve section. The two pre assembly sections comprise back and front preparatory/sub assembly sections respectively. Cut parts will be received from cutting section in rack A. The maximum permissible WIP in rack A is defined at one hour. Simultaneous feeding will start for back, collar, and cuff and sleeve section. Material movement for collar, cuff and sleeve sections will be in bundle form. Material movement at sub assembly section (front and back) and final assembly section will be in a single piece form. After operation number 11 (in back section), the pieces will be transferred to operation number 18 (in the front section) for matching. Maximum of one bundle is allowed between two work stations. Bundle size is kept limited to 15 pieces. Work stations number 11, 18 and 22 are intermediate super markets where intermediate WIP is allowed. Exhibit 1.5 highlights projected advantages of flow setup against traditional assembly line setup. Flow manufacturing is projected to give 12 per cent higher pieces per operator per day and one per cent improvement in SAM as compared to conventional assembly line manufacturing.
Develop Intermittent Supermarkets
A provision of intermediate supermarket (buffer) controls the flow of production & minimum sufficient inventory between processes.
Since it is not practically possible to design a continuous flow system, where a single piece flows from cutting section to packing section (largely on account of unbalanced production capacities in chained manufacturing system), a provision of intermediate supermarket is provided to control the flow of production. The provision of supermarket helps to control production, where continuous flow does not extend to upstream processes. It also helps to maintain minimum sufficient inventory between processes/sections to ward against contingency (breakdowns, absenteeism, etc.) and to hold the system together. In Exhibit 1.6, work stations number 11, 18 and 22 demonstrate intermediate supermarkets where maximum WIP is allowed. Exhibit 1.7 demonstrates supermarket buffer post cutting section that facilitates the flow of cut panels to sewing section. However, it is necessary to define and maintain buffer quantity at the supermarket stages, so that they facilitate the production flow in the event of contingency and do not turn into inventory stock points. It is recommended to design integrated individual finishing and packing stations for each sewing line with supermarket in-between assembly, finishing and packing. Finally, as lean manufacturing revolves around the philosophy of continuous improvement, further efforts should be directed in initiating Kaizen events for eliminating supermarkets where and when possible.
Depending on the ease the new configuration offers in production flow and operational control, it is for individual factory to decide on the layout that approaches closest to flow system. Efforts should be further directed in initiating Kaizen events for eliminating supermarkets where and when possible.
Conclusion
The exercise on dummy style has successfully demonstrated the methodology for developing flow manufacturing in apparel operations. It can also be highlighted that flow manufacturing can bring advantages such as single piece flow (assembly stage), leading to low WIP and reduced wastage.
(Flow Manufacturing aims for single piece flow system on all work stations. Prerogative for deciding between single piece and bundle system for each section depends on ease it offers for production flow and operational control. As a thumb rule, more the sections facilitate single piece flow, the more the layout conforms to flow manufacturing system, it is for individual factory to decide layout that approaches closest to flow system).