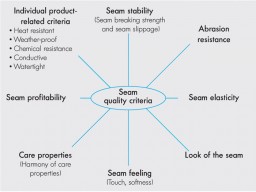
Quality of sewn products is only as good as the quality of seams. There are a few standard indicators to determine seam quality, like seam stability, abrasion resistance, elasticity and look. With the growing demand for technical textiles, the importance of a perfect seam is accentuated. There is a need to rework at the ‘basics’ so that quality of sewing is maintained. Amann Thread, on special request from Team StitchWorld, puts together the process parameters of a perfect seam.
Quality means performance, conditions, and properties. If you want to assess a seam under these aspects, you need a detailed requirement profile. Seams are tear proof, elastic, soft, watertight, weather-proof, easycare and can just be decorative…, depending on the given requirements. And they are always decisive for the product quality. Airbag seams, jeans seams, or upholstery seams – they all ask for different properties of the seam connections and thus have their individual requirement profiles. However, there are indicators that are true for almost all seams. The image above shows the most important standard indicators and gives examples for individual quality criteria.
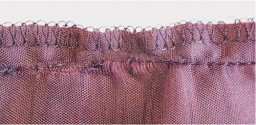
Seam stability
For assessing the seam stability, it is important to check the cross resistance (EN ISO 13935) and the seam slippage (EN ISO 13936). Seam breaking strength describes the resistance of seams to tensile stress on the seam, in crosswise direction. If a seam’s breaking strength is insufficient, the seams will tear during the later use. A well-known example from practice here are broken back seams on trousers. The seam slippage relates to the tendency of the warp and weft threads in a fabric to shift in cross wise direction to a seam under tensile forces. This is a fabric-related issue. A low seam shifting resistance leads to open seams, and possibly even broken seams. Many fashion fabrics show this problem.
An unfavourable seam slippage can be improved only marginally by changing the sewing conditions, for example through additional top stitching seams at the relevant seams, or the use of lap seams. Partly, it helps to use an additional non-woven interlining to reinforce the fabric in the area of the seam – an emergency solution, which is very time- and cost-consuming. The used sewing thread, however, does not have any influence on the seam slippage, despite various statements to the contrary. Basically, it is up to the fabric producer to improve the seam slippage.
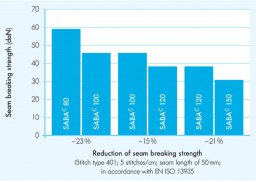
in accordance with EN ISO 13935
The seam’s breaking strength is determined by the fabric, the sewing thread, and the sewing parameters. The basic level of a seam’s stability is firstly determined by the fabric’s tensile strength (in warp, weft, and diagonal direction). Apart from that, the used sewing thread is the primary factor for the possible seam breaking strength of a seam – its raw material, strength, and construction. Cotton or polyester, fibre thread or multifilament construction, coarse or fine counts – the possible stability of the different threads varies extremely.
When choosing the sewing parameters, the stitch density, stitch type, and the thread balance in the seam have a great influence on the seam’s breaking strength. Increasing the stitch density by only 1 stitch/cm, for example, leads to a 25-30% increase of seam breaking strength. When comparing the most important stitch types for joining seams, the lockstitch and the double chainstitch, the double chainstitch is to be favoured under the aspect of seam breaking strength.
The seam abrasion resistance is one of the most important criterions for assessing threads behaviour in use as it characterizes the thread’s resistance to abrasion stress. The characteristic of the fabric is decisive for how flat or prominent a seam should be
Seam abrasion resistance
The seam abrasion resistance characterizes the thread’s resistance to abrasion stress in the seam. It is one of the most important criterions for assessing a thread’s behaviour in use. Seams are often exposed to great abrasion stress in buttonholes, exposed ornamental seams, seams on stone-washed jeans, cover seams on biking pants, just to name a few examples – are under great stress. Quite frequently, they show signs of wear after short use periods only, with a frayed seam pattern or totally worn and torn seams.
The seam’s abrasion resistance is determined by the fabric, the seam construction, and the sewing thread. The characteristic of the fabric is decisive for how flat or prominent a seam is, thus having more and more exposure to the abrasion stress. Fleecy and voluminous fabrics protect the sewing thread from rubbing, hard and glossy fabrics expose the seams more and thus increase the abrasion stress. Accordingly, the seam construction (seam and stitch type) influences the abrasion resistance. For example, lap seams for joining two material plies cause a more intense abrasion stress for the needle thread than inside positioned safety stitch seams. Thus, the looper thread in a double chainstitch is exposed to abrasion stress much stronger than in a lockstitch. However, the seam’s abrasion resistance is primarily determined by the sewing thread, and in this regard, mainly by the raw material, which determines its general resistance to abrasion.
There are big differences in a seam’s abrasion resistance depending on the raw material. The sewing thread construction and its strength do have some influence too, but it is much lower than that of the raw material. Corespun threads feature a better abrasion resistance than fibre threads, for example. Multi-filament threads are the best. Coarser threads tend to be more resistant to abrasion than finer threads. But this is tricky, too, because coarser threads are more prominent, thus increasing the abrasion stress which can even reverse the expected result. Then, the abrasion resistance of a finer thread is better again.
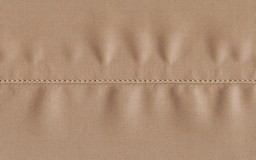
Seam elasticity
Seam elasticity means the elasticity and the behaviour of a seam under tensile stress in lengthwise direction. It is primarily determined by the thread reserve in the seam. The thread reserve refers to the amount of thread worked into a seam. It is determined by the type of thread as well as the stitch type. For example, under normal sewing conditions, a 1 m lockstitch seam uses 2.80 m of thread, while the same length of chainstitch and overlock seams use 4.80 m and 17.10 m of thread, respectively. Hence, chainstitch and overlock seams are more elastic in nature compared to the lockstitch seams.
Today, elastic seams are important for many applications which include undergarments, sportswear, swimwear, diving suits, etc.
With the availability of advanced features in threads, it is possible to produce elastic lockstitch seams.
Such threads provide an additional security reserve, thereby reducing the broken seams due to material overstressing.
Besides, Sewing thread, stitch density too, has an influence on the thread reserve and thus on seam elasticity. The greater the stitch density, the greater is the elasticity of the seam. A stitch density of 5 stitches/cm is considered standard, depending however on the chosen stitch type. For extremely elastic seams, stitch densities of 7 or 8 stitches/cm can be necessary.
Perfectly set thread tension is also a basic requirement for the greatest possible thread reserve in the seam. Too high thread tensions will noticeably reduce the quantity of thread in a seam, so that the seams will break in the length wise direction under very little stress. Lockstitch seams are especially known for this problem. At the same time, an unfavourable thread balance of needle and bobbin thread can reduce seam elasticity.
Special attention should always be paid to the needle thread tension, because the needle thread is the thread with the shortest travel within the seam in almost all stitch types, and therefore it is the weakest link as regards elasticity.
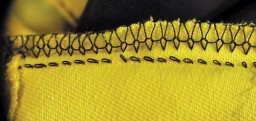
Look of the seam
The look of a seam can be assessed by everybody any time; there is no need for expensive test methods or special expert knowledge. Every customer knows very well if he or she likes the seam. This rather subjective evaluation makes the look of a seam a very special quality criterion. A good look of a seam depends on many factors. Often, one notices how the visual perception can be impaired only if one dislikes something. And there are many causes for this:
Seam pucker: A clearly rippled appearance, on one or both sides of a seam is desired rather seldom. Seam pucker is one of the most frequently occurring problems in the production of clothes. It can occur directly after sewing, during ironing or pressing, or shortly thereafter, along the seam or in specific sections of the seam. In practice, they are usually evaluated visually. Partly, a photo measure is used to facilitate evaluation.
Seam marks: Marks in the area of the seams visible on the outside of a garment are a well-known production problem with fine fabrics. They are caused by seam allowances or sewing threads that leave marks through the ironing of the seams or the pressing of joining and overedging seams.
Unfortunate matching of sewing thread and fabric: Well-known in practice here is the unfortunate matching of the sewing thread colour. But also a thread’s construction and strength often does not emphasize a fabric’s or model’s character.
Unfavourable thread look: An open, coarse fibre pattern gives a scruffy impression and is usually disliked. Through rubbing stress, sewing threads can be worn to threads. Individual fibres will then stick out from the thread and cause the scruffy look.
Unfavourable stitch looping and incorrect thread balance: This makes an uneasy seam pattern, which is not acceptable, at least not for the visible seams. A well-known example here is the incorrect stitch-forming with the lockstitch. With this stitch, the looping of the needle and bobbin thread should take place in the centre of the material plies; in practice the picture is often different.
Diverging seams: Diverging or loose seams are a sign for production errors, and you don’t have to be an expert to know that. This occurs mostly on joining seams that are exposed to intense stress during use, for example the back seams on trousers. Diverging seams show where the stitches are formed between the edges of the seam. Under tensile stress, in crosswise direction to the seam, the sewing threads are visible, looking like a ladder. Possible causes are an insufficient thread formation, a low thread tension or a low stitch density.
Seam touch
Many garments are worn directly on the skin; many seams are touched by our hands every day; so a seam’s touch cannot be left out as a criterion for the seam quality. It includes all of the touch feel perceptions and this is what is interesting regarding seams. In practice, this quality indicator is just called “touch”. In sportswear, flat seams and a favourable touch are of extreme importance. A good example is biking pants.
A seam’s touch depends on the fabric, the seam construction and the sewing thread. The fabric determines how well the seam is bedded in the material. The seam construction determines the form of the seam. And in case of cover seams and overedge stitches, it defines the width of the seam. With all stitch types it influences the height of the seam, together with the sewing thread. Its influence becomes clear when comparing lock stitches with double chain stitches. The double chain stitch features a significantly more prominent seam through its bobbin thread chain.
The greatest influence on a seam’s touch has the sewing thread, and this is also the factor that can be changed most easily. Strength, construction, and raw material of the sewing thread play a role here. By varying these three parameters, one can create the most different touch feelings. Fine polyester bulk yarns make a different seam feeling than coarse polyamide multi-filament threads. Spun cotton threads create a different touch than braided polyester threads. Most often, the change of only one parameter leads to a clearly different touch feeling.
In case of covering chain stitches, the cover and bobbin threads are extremely important for a good touch feeling, because these are in cross wise direction to the seam, and their share of the seam surface is the greatest one. For this reason, bulk yarns are used, if they can fulfil the requirements of a garment’s later use. They make soft seams due to their voluminous and soft character. Practical tests have shown that the needle thread has a remarkable influence on the seam’s touch, too, because of the loops showing on the underside of the material. If the seams need to be extremely soft, one should therefore think about the needle thread to be used as well.
Like no other criterion, the touch of a seam can be evaluated by manual tests of different seam samples only.
Seam care
Determining the quality requirements on a sewing thread’s care properties is easy: The sewing thread must correspond to the care requirements of the fabric. Outer fabric and sewing thread must match.
Also for contrast colours or for extreme care conditions, for example for hospital textiles or workwear, the seam’s care durability must be tested individually.
Seam profitability
On the question of whether the seam profitability is a quality criterion, there have been many arguments. Without doubt, however, the seam profitability is of great significance for the producers. It is an important criterion when designing and deciding on the seam. For production, it is extremely important that quality seams can be realized economically. So, in this respect, the seam profitability is a quality indicator. By choosing the right processing parameters and the right sewing thread, the seam profitability can be influenced.
Profitability in seam processing depends on the following calculatory factors:
– Individual sewing thread costs (Quantity and price),
– Labour costs + non wage labour costs,
– Operating supplies, for example sewing machine needles,
– Costs of workplace (Investment costs),
– Energy costs per work place (Power, compressed air, etc.).
The costs incurred by the sewing thread in addition to the mere production costs, must also be taken into consideration. For example through the fact that threads breaks can occur when using low quality threads, for example through knots, unevenness, etc. which necessarily leads to machine and automate downtimes, and thus to higher production costs and a lower productivity.
Individual product-related quality criteria
In addition to the standard quality criterions, there are numerous product-related requirements.
This applies especially for the production of technical textiles. When function is decisive, requirements on sewing threads are most different. Here are some examples of this great variety:
– Heat resistant seams for heat protection clothing,
– Weather-proof seams for outdoor textiles,
– Chemicals-resistant seams for chemical protection clothing,
– Conductive seams for conductive textiles,
– Waterproof seams for rainproof clothing,
– Non silicone sewing threads for special applications in the production of filters,
– Absorbable seams for surgical applications.
The more detailed the application profile, the better the chance for perfect seam quality.