A bra or brassiere is one of the most critical sewn products. Unlike other apparel and textile products it is not just meant to cover the human body, rather it is highly engineered and thoughtfully designed to support the breast for health reasons. To ensure the perfect fit, sewing precision is critical, and can be gauged by the fact that European companies expect bras to be within 3.175 mm of the desired measurement. And if chosen/designed incorrectly can cause minor level stress and depression, and breast cancer in extreme cases to the wearer. However, a bra is not just sought for its great utility but also for that desired look, feel and occasion. Team StitchWorld with Chandrajith Wickramasinghe, a Sri Lankan expat, with a decade’s experience of working with MAS holdings, and organizations like Victoria’s Secret, MAST and M&S, present a complete bra sewing process paradigm, balancing both the utility and finesse…
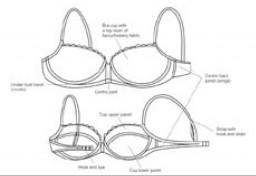
The broad categorisation of a bra is not only based on its type of construction and function but also on the basis of the fabric used and whether it is with or without foam. A bra – whether seamless, structured, strapless, with foam, without foam, padded, moulded, wired, non-wired – is constructed on the foundation of the four building blocks, and they are – bra cups; the under bust band or the centre front; the centre back panels; and the straps. Among hundreds of variations of bra, the cotton bras are the most popular and preferred by women all across the world.
It is said that 30-35 different parts are used to construct a bra. Embellishments with many types of body fabrics like a stabilizer fabric (polyester warp knitted non-stretch fabric) for cup seam and centre front, inside cup fabric, cup covering fancy fabric; various types of elastics for under-bust band, underarm region and strap besides that hook & eye, two pairs of ring & slide, bow, label and most importantly foam.
Preferably, a polyester warp knitted fabric is used for its unstretchability in a very small amount as a joint between both the cups, to impart the breasts ‘still’ shape, whereas a material with good stretch is used as the centre back panels of the bra for ease of fitting and wearing. A fancy bra usually has embroidered or lacy fabric used on the outside of the bra cup and cotton or blended fabric is preferred for high comfort and breathability in the inside as it comes in direct contact to the body.
[bleft]Raw material cost is 55 per cent to 60 per cent of the total FOB of the bra, which starts from a basic US $ 4.5 and depends majorly on the type of fabrics, trims used and their sourcing.[/bleft]
Foam which is moulded to give bra cup the precise shape of the breast is made of polyurethane although widely used in various textile and apparel products. It is specially processed before being used as a bra cup foam to prevent it from the gradual yellowing, which also affects the fabric in contact with outer and inner surfaces of cups. The ‘Stay White’ laminated foam is most preferred as bra cups and is used by all leading manufacturers for white or light coloured bras, whereas for dark coloured bras, grey or charcoal coloured foam can be used, since it is cheaper than ‘Stay White’. The foam is also selected on the basis of its ‘breathability’; the lower the density, the more the breathability. The optimum density of a foam to be used for bra cups is 35 kg per cubic metres. With recent advancements, a lot of viable alternative for polyurethane foam have surfaced with far better breathability, sweat absorbency, lighter weight and with reduced thickness, for example Spacer fabrics, Fibre foam, Memory foam, Biofoam, foam with already inserted under-bust wire and many others.
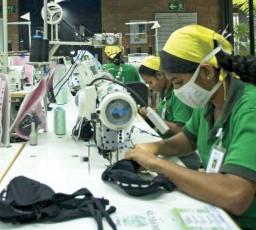
Before giving the shape to the foam it is laminated with fabric on either one side or both sides, depending upon the type of covering fabric. It can be laminated on both the sides simultaneously, but since inside fabric is usually a cotton blend and the outside one being polyester with 13 to 17 per cent spandex for comfort and flexibility, it becomes impossible to mould all the three together at a common pressure and temperature, as both the fabrics have different melting points. After laminating the foam with the cotton fabric, it is cut into rectangular blocks and moulded according to the desired cup shape. Usually, two cups are produced from a single foam block. The outside synthetic fabric is moulded separately and then stitched on to the moulded bra cup. The fabric is stretched at the time of moulding, hence is placed on cooling moulds for about 2 to 4 hours as it is necessary for the fabric to be fully-relaxed before being cut. Plastic panels in the desired cup shape are used for cutting the outside cup fabric. Foam moulding and cutting is an entirely separate department, however fabric moulding and cutting can be made a part of the sewing line for pursuing a lean manufacturing setup but is not done due to high operating and capital expenditures. Also the foam moulding department has to be fully dust-free to avoid dust moulding with the white foam.
[bleft]A bra is all about the fit and hence has very low tolerance levels. European companies expect bras to be within 3.175 mm of the desired measurement.[/bleft]
The bra cups (foam) are moulded in dye-cast moulding machines. The moulds can be changed according to the size of the cup to be prepared and are also responsible for altering the density of the foam. The whole process is dependent on the temperature, pressure and timing, and out of these three, the temperature is the most critical as it can be more or less depending on the fabric used; in case of polyester the temperature applied is between 1800C to 2100C. Similar moulding machines are also available for moulding the outer fabric covering. Unlike cost effective Chinese and Taiwanese machines available for moulding foam, the fabric moulding machines are generally expensive. Optotex Foam is one among few companies which has an exclusive range of fabric moulding machines, while Newpad from Taiwan is for moulding laminated foam.
Fully-finished and customised cups are also available from various lingerie accessory suppliers in India like Kotak Overseas, Mumbai.
[bleft]The sewing content can range from 8 to 30 minutes depending on the intricacies involved, while a basic bra has only 10 components it can go up to 35 depending upon the style. [/bleft]
Manufacturing Process
The cutting of bra fabric is generally done by dye cutter or band knife or in case of larger volumes computerized reciprocating knife cutter, but only after the fabric has been ‘relaxed’ by following appropriate shrinkage control methods. This is necessary as the fabrics have high spandex content and the tolerance levels being very tight, while pre-shrunk fabrics would have the same dimensions throughout their lifespan.
As bra patterns are very small parts and require absolute accuracy to cut, straight knife and round knife cutting is generally not advised. Also one bra may consist of multiple types of fabrics, laces and accessories, therefore small separate markers are prepared for different materials. Again due to small and several pattern components (multiple size and styles in same marker), very efficient markers can be done, as the small parts are easy to adjust on the marker, resulting in high marker efficiencies.
[bleft]• Foam for bra cups is selected on the basis of its breathability, which further depends on the density of the same. The optimum density of the foam to be used in a bra should be 35 kg per cubic metre.
• Foam is specially processed before being used as bra cup foam to prevent it from gradually getting yellow, which also affects the white or light coloured fabric in contact with outer and inner surfaces of cups. However, in case of dark coloured bras, grey or charcoal coloured foam can
be used.
• Optotex Foam is one among few companies which has an exclusive range of fabric moulding machines, while Newpad from Taiwan is for moulding laminated foam.[/bleft]
In the entire manufacturing process it is the effective bundling and marker management which is the most tedious process all because the parts of the bra of different sizes look quite similar, it is important to ensure that they do not get mingled together, as different cut parts may get attached to a different size set. To solve this problem, manufacturers devised a special storing system similar to ‘pigeon holes’. A pigeon hole table has big holes on its surface with a bag under each. The setup can be used as desired – a single pigeon hole can be used to store all the parts or components of a particular size for a bra or 3-4 pigeon holes can be used to store different patterns of the same bra. Later all the bags are segregated and all the parts of the particular size from all the markers of different fabrics are collated for final bundling.
This is helpful as at least 4 different types of fabrics (used in a single bra) in 5 to 6 different sizes are cut in the same marker and if colour variation exists, then it is very near to becoming a paradox. Storing them this way minimizes the likelihood of parts getting mixed up. This whole aspect of accurate and precise bundling highlights the importance of visual control to the whole area, so as to let know or convey the operators visually about the SOPs along with the do’s and don’ts.
Unlike bundles made for sewing other apparels, a bundle of the bra is made of sub-bundles for bra cups, cradle, wings and centre front panel. The operator has to open the main bundle, take out the bundle he/she is supposed to work upon and leaves the rest of the bundle untouched,
reducing the wastes of transportation and storage (temporary inventory).
Subsequent to bundle preparation, all the bundles (as per the daily production target of each line) are stored in a Kanban table placed in front of every line 1 to 2 hours before the start of the line production and no bundles are added during the day. The Kanban table has sections for storing the garment bundles and the trims and accessories.
[bleft]For accurate and precise bundle management, bra manufacturers around the world use Pigeon Hole tables with big holes and a bag attached under each, for storing all small parts and components of a bra.[/bleft]
The sewing lines of a bra operate on a simpler version of the progressive bundle system with a maximum bundle size of 12 bras, maintaining a very low WIP, with operators either seated side-by-side or face-to-face. The trims are fed to the sewing lines using Kanban System, but if the bra has laces and ribbons, then they are supplied with the final bundle only. Most critical on the sewing floor is the presence of various gauges and attachments for not only deskilling a specific operation but also for helping operators sew small and critical seams. Intervention like magnets and cardboard guides are used for limiting the dimensions of a seam. While passing the bra cups to the sewing line, a ball might be inserted in the cups to maintain its shape.
[bleft]In a fabric width of 1.5 metres, the consumption for a typical bra having five components, namely side panel; cup upper; cup lower; cup joining panel; and back panel is only 10 cm.[/bleft]
More than the equipment, it is the skill of the operator which is critical to sewing; it is their dexterity which makes them handle small parts effectively. What is required is the swiftness of the operator to sew, turn and stop every few inches, and this is one of the reasons that female workers are more suited for bra sewing and also they are very focused and smart workers. Also since the handling time is more than the sewing time in a bra sewing line, workplace and industrial engineering becomes of utmost importance for streamlining in-line material flow.
[bleft]When marker is prepared for sizes 28-30-32-34-36 in a ratio of 4:6:10:6:4, in a fabric width of 1.5 metres, one can achieve marker efficiency of 80% or higher.[/bleft]
The construction of the bra is primarily joining the cups with a central fabric, sewing of shoulder straps and the support underneath the cups, which usually works in combination with the shoulder straps to hold the breast. The shoulder straps should not only be stretchable and comfortable, but also fixed with utmost strength to the cups and centre back panels. Whereas the centre fabric panel between the cups should not be stretchable at all so as to keep the cups in position all the time.
Since finishing or ironing is not needed as the bra would again be crushed while packaging, a clean set-up and dry-head sewing machines are recommended.
Production and Manpower Planning
A total of 27 sewing operators with a person each for checking and packing, are required to produce 883 13-minute bras per 8-hour shift. Wherever applicable either one operator does two operations (for e.g. in top stitch, the elastic has been merged with attach hook & eye with label) or one operation is done by more than one operator (for e.g. centre front panel preparation is done by 2 operators). Additional time has been added to all the sewing operations for hand work.
Production Layout
In a conventional manufacturing setup, separate batches are made for bra cup preparation, cradle & wing preparation and the final assembly. This type of sewing setup is usually practiced by lingerie manufacturers and is not lean. Waste of temporary inventory (storage) is very dominant in this setup, i.e. three batches requiring 6 storages for the input and the output. Due to the same reason a lot of wastes also happen in transportation of goods, or waiting time for parts on the sewing line at times, as the operators are also not placed in the right order to optimize the material flow within the line.
In the lean sewing flow, all processes have been made a part of a single line, however it would not be possible at times due to the space constraints but every effort should be made to minimize the material transportation on the sewing floor. Also the sewing line starts with centre front preparation and after the cradles and wings have been prepared, the bra cups are worked upon – unlike the general perception of commencing bra sewing with cup preparation.
The final checking along with tagging, folding and labelling have also been made a part of the assembly line only. After the bras have been placed in cartons, they are directly sent to the finished goods warehouse for shipment. A stable WIP of 12 bras is maintained throughout the line. It has been assumed that the machine uptime is 97 per cent of the daily 8 working hours and the right first time percentage is 98 per cent. With the lean sewing setup discussed, 82 per cent operator efficiency can be achieved.
Sewing Machines for Bra Manufacturing
Against the general perception that bra sewing requires highly automated solutions because of it being an engineered product, it just requires basic sewing machines with few additional features and extensive use of attachments and work aids for deskilling the overall sewing operations. The common features across all types of machines are semi-dry heads, light-duty and direct-drive motors.
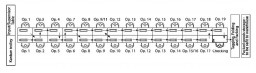
wings and centre front cut parts. So the operator would only open the bundle of the operation to be done by him/her.
Zigzag Lockstitch for the stretch and finish
Providing a unique look with extra stretch, comfort and fit in certain areas, zigzag is the second most important stitch-type after lockstitch in sewing a bra. Zigzag machines comes preloaded with around 20 different zigzag, T-stitch, blind stitch and cover stitch patterns grouped into 14 different types, and a maximum of 99 patterns can be stored with the self-pattern input function. A single unit of a Zigzag sewing machine is extremely versatile and can perform straight, standard zigzag, 2-step zigzag, 3-step zigzag, scallop and blind stitch. As a result, the machines are available for a far wider range of applications. Fine stitches of 1.3 mm to 10 mm width can be produced with the help of the innovative Zigzag sewing machines. The rotary hook used in the machines is devised to form a thread loop at uniform intervals from side to sides by adopting a rotary hook shaft offset mechanism, which not only provides the fine sewing quality but also prevents the thread breakage and stitch-skipping problem.
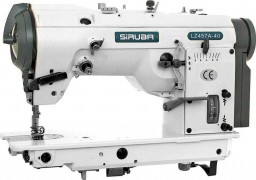
Pattern Tacking for extra-strong seams
Bartack is specifically done on areas which require extra strength like the bra cup and strap joining as the breasts are supported by this sole joint. The bartack machines can achieve a maximum sewing speed of 3000 stitches per minute, enhancing the start-up speed at the beginning and ending of sewing, as well as the speed of thread trimming, thus reducing the total cycle time and enhancing productivity.
In addition to the high-speed sewing performance, the machine’s starting, stopping, thread-trimming and automatic presser lifting speeds have been increased to significantly shorten total cycle time and are equipped with a vertical presser foot specially for bra. The machine that comes with 50 pre-fed patterns and can store up to 200 bartack patterns. All being computer-controlled the stitches can be customised for quality and look to the finest of detail.
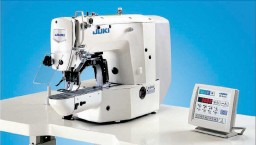
Single Needle Lockstitch for strength and stability
Lockstitch is majorly used in joining the whole bra for its strength and stability. All the machines are made keeping in mind the ergonomics required specifically for sewing a bra, for example all types of levers and clutches present in a basic lockstitch machine are repositioned specifically for bra operation and the presser foot can be lifted to a minimal height of just 15 mm, unlike regular lockstitch machines. The machines are also equipped with smooth and swift under-bed trimmers, which also prevent the nuance of ‘Bird’s Nest’ formation at the start of sewing, common in machines with under-bed trimmers. With the ability to sew at the speed of 5000 RPM, the machine is equipped with features like reverse feeding, auto-thread trimmer and thread wiper.
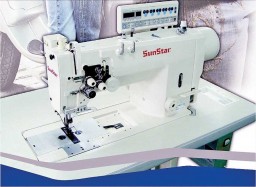
Double Needle Lockstitch for tape and wire attaching
Double needle lockstitch is majorly used for giving extra strength to tape and wire attaching operations and also for reducing the time consumed in doing seams requiring two parallel lockstitches. For effective control over the delicate lingerie fabrics, the presser foot can be lifted by a very minute amount by adjusting the eccentric pin located in the presser lifter lever section, thereby reducing the pressure on the fabric, which helps sew shaggy and elastic fabrics. The thread trimming mechanism in the machines has a wide operating facet, which enables uniform thread trimming even when the sewing thread width keeps varying, barring the need to change the thread trimmer’s setting with the change in the sewing thread.
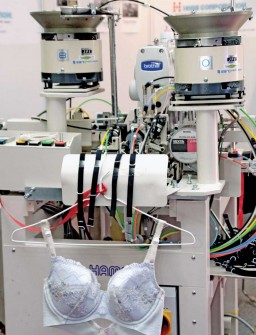
Special Operation Machines for Bra Strap Preparation
The MHA-600BB Bra strap sewing machine from Human Apparel Solutions (HAMS) Japan, has combined the whole process of cutting the strap, inserting the 8-shaped ring, closing its end by sewing and then inserting the O-shaped ring in a single operation, that too in an unbelievable time of just 5 seconds, producing up to 4600 straps in a single day. The machine has in-built photocells which senses the required length of the strap and actuate the cutter to cut the strap at the required length, minimizing the labour requirement to just a single operator from three operators. This machine can also incorporate functions of detecting thread shortage, ring metal shortage, tape material shortage and tape seams. The machine although being a high-end automat is simple in operation, thanks to its Japanese design, and with a few gauge changes the machine can operate on straps with a maximum width of 18 mm. The standard life span of the machine is 10 years, and the ROI can be achieved in about 5 years. Due to the nature of the machine, it is placed not on the sewing floor but rather in the trims store, where straps are prepared size-wise and allotted to the lines.