Work In Progress (WIP) is one of the fundamentals in building a ‘Lean’ environment in a business. It is often an overlooked part of the practice to reduce lead times and increase factory performance. WIP, in a very simple parlance, means the number of garment or parts made during production in the factory at any one time. For a garment manufacturer, WIP would include fabric that has been spread, part sewn garments, through to finished garments, which may have been packed but not booked for finished goods warehouse. This article discusses the importance of WIP on the shop floor and its effects on the functioning of the factory.
Traditional methods of organizing workflow are slowly losing charm as factories face the complexity of multiple styles, larger volumes, lower profit margins and shorter lead times. Fast React Systems is a global supplier of software-based solutions for the apparel, footwear and textile industries. With over 30 installations in India itself, the company is enabling businesses to reduce lead times, WIP and inventory, to improve productivity and live up to customers’ demands for fast and accurate information. The author, Simon Gibson, is MD of Fast React Asia and has been involved in apparel manufacturing for 26 years holding management positions in Industrial Engineering (IE), production management and consultancy in UK and Asia.
[bleft]WIP is one of the Key Performance Indicators which directly influences various areas of production. It is pitty that many factories either ignore or do not know its importance resulting in overproduce and wastage of both time and resources[/bleft]
Work in Progress (WIP) of garments can be expressed in the number of pieces by simply recording daily production figures between each process and accumulating the difference between sequential processes. For eg. if we have to cut 10,000 pieces but sew only 6,000 pieces, then WIP in sewing will have to be increased by 4,000 pieces on that day.
The total amount of WIP in each department (e.g., Cut, Print, Sew, Wash and Pack) should be calculated and reported on a daily basis. It is, probably, most easily measured and controlled by expressing the WIP in days by dividing the total WIP in pieces by the average production target for a day.
Table 1 shows a simple daily WIP status by individual process for 18,500 pieces. With a daily output of 3,000 pieces, it will take 6.2 working days to complete all work.
WHY IS WIP IMPORTANT?
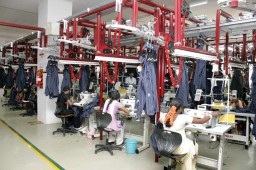
WIP should be considered as one of the KPIs (Key Performance Indicators) of the production manager as it has a significant effect on a number of key areas. Effective Use of Working Capital : WIP costs money (material, labour and overheads) to produce; and excess WIP means an excess of working capital tied up in a resource that is not adding any value.
Storage Space and Housekeeping: Higher the WIP, more the storage space required which is provided by trolleys or racks that are used to store garment parts in a tidy manner. With an increase in WIP, more storage equipment will be required. It also results in work waiting in racks or trolleys for a longer period, thereby increasing possibilities of dirtying and crushing of the garment parts. Consequently, additional non value added costs are incurred for pressing and cleaning these parts. In some cases, excess WIP can lead to more serious issues such as blocked gangways and fire exits. In contrast, this space could be put to more productive use, i.e. adding more sewing lines, while saving on cost and control on quality.
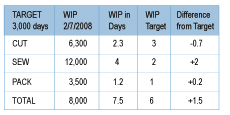
Quality Control : When it comes to quality, high levels of WIP results in problems being created much before they are detected by roving or final QA, and therefore increasing the chance of defects and rework.
Response to Customer Needs and Risk : WIP ‘queueing’ also significantly reduces flexibility and speed of response to the market demand. Less WIP means, cutting can be closer to the final delivery giving the buyer more chance to make last minute changes to style, size and colour breakdowns, based on the latest market feedback. In today’s quick change fashion environment, high levels of WIP could mean that you are making the wrong product. Compared to a roll of fabric and finished garment, WIP, i.e. partly-made garments, have a high cost but low value. So, carrying high levels of WIP is financially risky.
Production Control : Another drawback with high levels of WIP is that it provides a false sense of security. Problems are less obvious, the need for solutions is less urgent and often overlooked. High WIP levels make it harder to find and quickly process an urgent order or size/colour selection through the production system.
WHAT IS AN ACCEPTABLE WIP LEVEL?
[bleft]It is very essential to keep the WIP under your control. At various stages it requires regular monitoring and planning. Fastreact, an integrated apparel specific planning system, can provide all these features[/bleft]
For such an important business KPI (Key Performance Indicator), it is worrying that many factories simply do not know how much WIP they have at any point of time let alone try to control it.
The control of WIP is not seen as a priority. A systematic approach is lacking. So, each department simply works to its own ‘perceived’ priorities, typically overproducing and carrying unnecessary high levels of WIP. Acceptable levels of WIP will vary according to a number of factors:
- Product type – A more complex product with more processes, for example sportswear with embroidery, printing, higher sewing SMV, will require a higher level of WIP than a simple product such as underwear.
- Production System – A bundle system will require more WIPs than a modular or UPS (Eton, etc.) system.
- Subcontracting – The need to subcontract processes such as printing or washing will increase WIP levels.
- Management/Supervisor Capability – The ability of the management and production floor supervisors should be such as to react and solve problems quickly.
Typically in factories that do not control WIP, we have seen that the actual WIP level could be between 18-24 days, i.e. 3 or 4 weeks worth of work! In a modern well-managed factory, the optimum level of WIP would typically be between 4 – 12 days depending on the factors above.
HOW TO CONTROL AND REDUCE WIP?
There are seven steps to control the WIP.
1. Educate – It is important to remember that supervisors and workers typically see high levels of WIP as a good sign, as they see they have plenty of work, are productive and have a good opportunity to produce bonus. Before starting WIP reduction and control, it is essential to educate the production team about the whole WIP issue.
2. Measure – The amounts of WIP currently in the system has to be measured. A daily report should be made to identify the WIP level by order/ production department after each day’s production update.
3. Target – For each production process/product type/ factory, a target should be agreed on for the amount of WIP required, see Table 2. This can best be expressed in days (based on the current output target) and should be sufficient to enable production flow allowing time for issues to be resolved before WIP shortages occur. If current levels are much higher than the set target, a gradual reduction over a period of a month is better than a rapid one off reduction.
4. Plan and Communicate – To achieve targets, clear schedules must be provided for each production process. These targets are worked backwards (e.g. cut, embroider) or forward from the sewing schedule (e.g. wash, pack). They should reflect the output requirements of the sewing plan but will be x days earlier or later (depending on target of the WIP level). Before the final plan is issued, capacity vs. load of all processes must be carefully checked to ensure that the plan is achievable. For example in a cutting room, the workload will increase dramatically if a high proportion of the orders are striped or check fabric, and require pattern matching.
5. Monitor – This means to compare Actual Target against the Daily Target. Total WIP levels should be monitored by calculating and reporting actual WIP levels against the Target by process for each factory, as shown in Table 2. This Table shows a Daily WIP report format showing actual WIP and variance against target. Cutting WIP is a little low but this is not so relevant in comparison to Sewing WIP, which is alarmingly high, i.e. twice the agreed target. This needs to be investigated. For example: If sewing is achieving production target, it means cutting has been overproducing and should reduce output until the WIP is at target levels.
6. Control – This is to identify areas where there is too much or too little WIP and take action to correct. This is easy on a department to department basis but should also be done on an order by order basis, to identify orders where WIP may not be sufficient to meet the plan and hence the delivery schedule.
7. Improve – As with any KPI, the goal should be to achieve the target consistently and then aim for continuous improvement. Achievement against target should be plotted overall and by process/factory in order to identify trends and areas where further savings could potentially be made.
THE FINANCIAL BENEFITS
Of course a WIP reduction project like any other project requires management commitment and time. The good news is that a simple calculation of the financial benefits in reducing working capital alone provides a compelling reason why WIP management should be a priority.
Consider a typical factory producing 15,000 pieces per day, with an average FOB value of $ 5 per garment.
- One day of WIP costs $ 56,250 (assuming 75% of FOB value)
- 14 days WIP ties up to $ 787,500 in working capital.
A 20% reduction in WIP, i.e. reduced by 2.8 days, would reduce the working capital invested by $ 157,500.
Plus more and more benefits outlined in the Why is WIP Important section such as more floor space, less creasing, improved quality, etc.
CONCLUSION
An important point to stress is that production management, supervisors and workers typically see high levels of WIP as a good sign. In their eyes they only see that they have plenty of work and are productive. As such they are nervous when we say we must reduce it as they believe it may hurt productivity.
This is a valid point. Before starting a WIP reduction programme be aware that it will only be successful if systems are put in the right place to ensure good planning and that accurate, and achievable targets are set and communicated. Equally important is fast and accurate daily reporting of any WIP shortage before it affects the factory workflow.
Given the benefits, it makes good sense for any manufacturing business to invest not only its time and effort on achieving WIP control, but also invest in systems that greatly simplify the process of scheduling, capacity management, reporting and identifying problem areas. An integrated apparel specific planning system like Fastreact can provide all these features. As calculated above, a modest and achievable reduction in WIP in turn reduces working capital and can provide a return on investment for a system like Fastreact in just a few months.